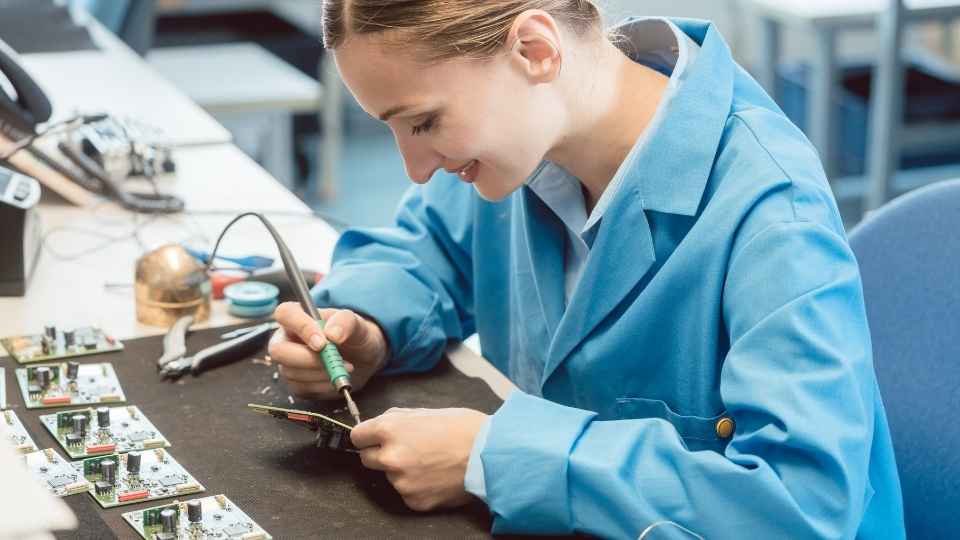
In today's rapidly evolving manufacturing landscape, industrial robots have emerged as a driving force behind the transformation of traditional processes. With advancements in robotic arms and automation, these machines are revolutionizing assembly lines and enhancing overall efficiency and productivity.
However, this technological revolution also raises questions about the impact on job roles and required skills. In this article, we will delve into how robots are reshaping modern manufacturing processes, exploring their implementation across various industries while discussing future trends and challenges in the field of industrial robotics.
Key Takeaways
- Industrial robots revolutionize production by improving efficiency, accuracy, and productivity.
- Automation optimizes workflow and achieves higher output levels in less time.
- Advanced automation technology reduces labor costs in manufacturing.
- Robots revolutionize assembly lines by increasing efficiency and reducing errors.
The Rise of Industrial Robots in Manufacturing
The rise of industrial robots in manufacturing has revolutionized the way companies produce goods and services. These advanced machines have significantly impacted the efficiency, accuracy, and productivity of modern manufacturing processes.
By automating repetitive tasks, robots have freed up human workers to focus on more complex and creative aspects of production. Industrial robots are equipped with sophisticated sensors and algorithms that enable them to perform precise movements with high speed and accuracy. This level of precision ensures consistent quality control throughout the manufacturing process, reducing errors and waste.
Moreover, these robots can work continuously without fatigue or breaks, resulting in increased productivity levels for businesses. The integration of industrial robots in manufacturing has not only transformed traditional assembly lines but also allowed companies to meet growing consumer demands while maintaining cost-effectiveness and enhancing overall operational flexibility.
Advancements in Robotic Arms and Automation
Advancements in robotic arms and automation have revolutionized manufacturing processes by offering increased production efficiency and reduced labor costs.
These technological advancements have allowed industries to streamline their operations, optimize workflow, and improve overall productivity.
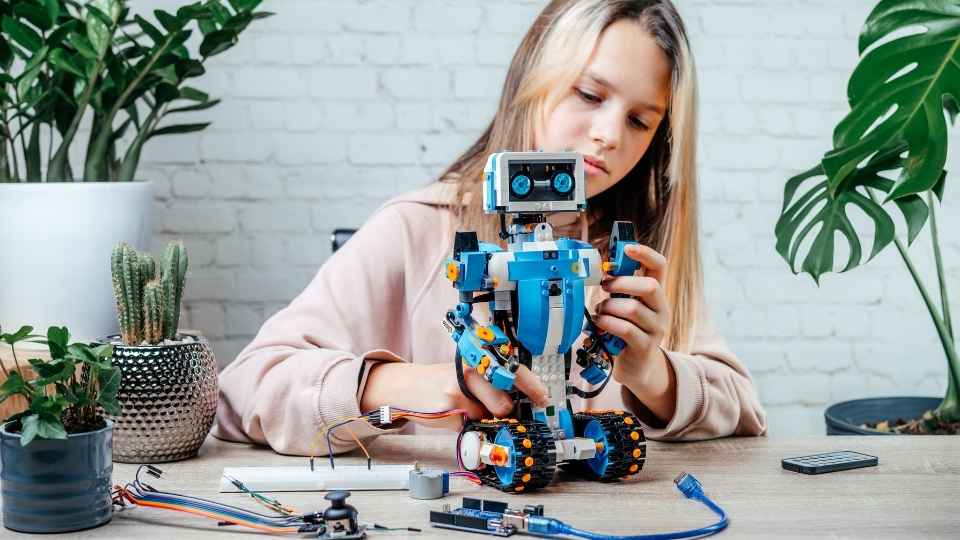
With the ability to perform repetitive tasks with precision and speed, robotic arms have become an invaluable asset in modern manufacturing facilities.
Increased Production Efficiency
Enhanced production efficiency is a key result of incorporating industrial robots into modern manufacturing processes. These robots are designed to perform repetitive tasks with great precision and speed, reducing human error and increasing overall productivity. Through the use of advanced sensors and programming, these machines can operate 24/7 without the need for breaks or rest, leading to continuous production cycles.
Industrial robots also have the ability to work in hazardous environments that may be dangerous for humans, further improving efficiency by eliminating potential risks and delays caused by safety protocols. By automating various stages of production, companies can optimize their workflow and achieve higher output levels in less time.
This increased efficiency has significant implications for manufacturers in terms of reduced labor costs.
Reduced Labor Costs
By incorporating advanced automation technology, manufacturers are able to significantly reduce labor costs while maintaining high levels of productivity. This is achieved through the utilization of industrial robots that can perform repetitive tasks with precision and speed.
The benefits of reduced labor costs go beyond financial savings for manufacturers; they also have a positive impact on workers and society as a whole. Here are three reasons why reduced labor costs through automation evoke a sense of freedom:
Increased job satisfaction: When mundane and repetitive tasks are automated, workers can focus on more meaningful and fulfilling work that requires creativity and problem-solving skills.
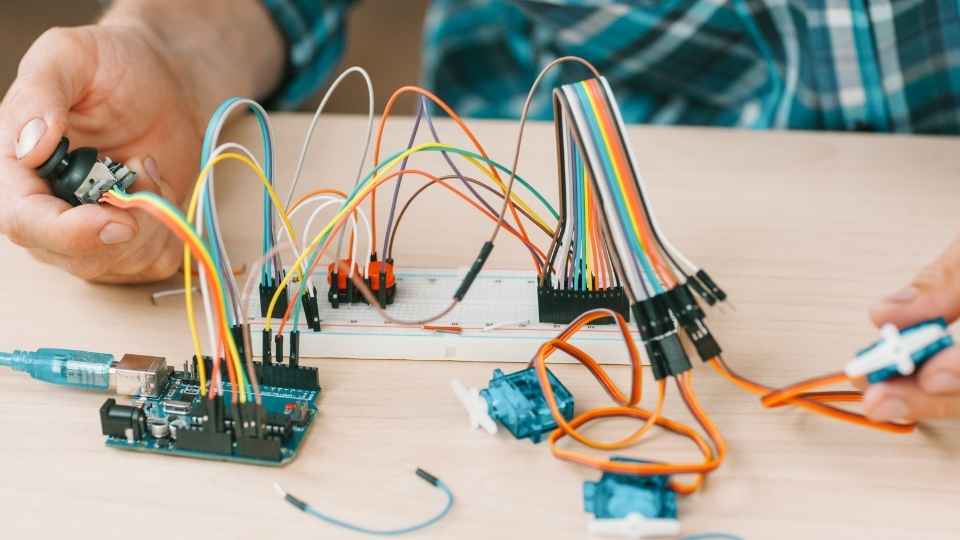
Enhanced work-life balance: With fewer hours spent on monotonous tasks, employees have more time for personal pursuits, family, and leisure activities.
Economic empowerment: Reduced labor costs allow companies to invest in employee training programs and provide opportunities for skill development, leading to career advancement and increased earning potential.
Robots are revolutionizing assembly lines by streamlining production processes and increasing efficiency in modern manufacturing. These automated machines have transformed the traditional assembly line model, allowing for higher productivity, reduced errors, and improved safety. With their precision and speed, robots can perform repetitive tasks with utmost accuracy, minimizing human error and maximizing output. Furthermore, they can work continuously without the need for breaks or rest periods, resulting in uninterrupted production cycles.
Robots bring freedom to manufacturers by reducing dependence on manual labor and enabling companies to allocate resources more efficiently. By automating tedious and repetitive tasks, businesses can reallocate human workers to more complex and creative roles that require critical thinking skills. This enhances job satisfaction while also driving innovation within the workforce.
How Robots Enhance Efficiency and Productivity
Robots have proven to be valuable assets in enhancing efficiency and productivity in various industries.
By streamlining production lines through automation, robots eliminate bottlenecks and optimize workflow.
Additionally, their precision and accuracy significantly reduce human error while their high-speed capabilities increase output rates.
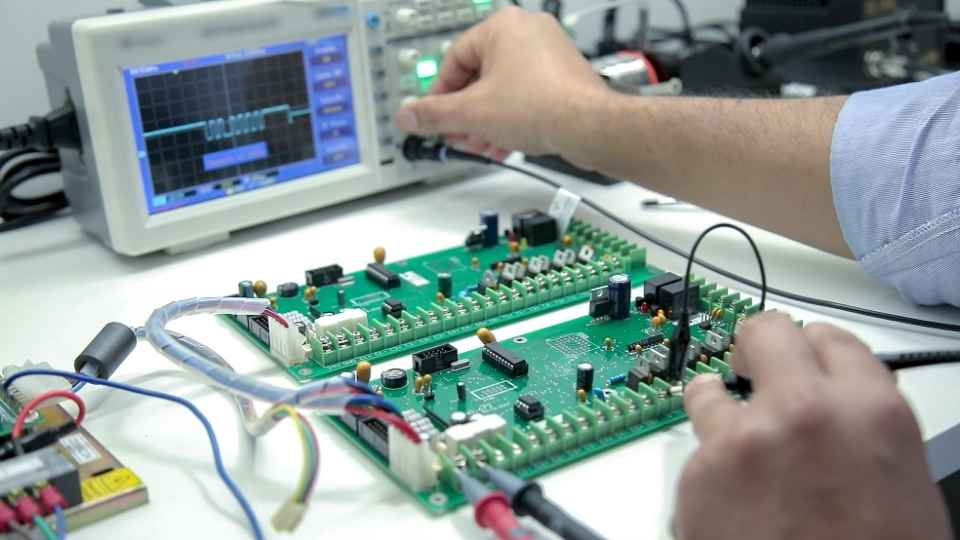
This ultimately leads to improved overall efficiency and productivity.
Streamline Production Lines
The implementation of advanced automation systems has significantly enhanced the efficiency and productivity of modern manufacturing processes, particularly in streamlining production lines. Industrial robots have revolutionized the way products are manufactured by offering numerous benefits such as increased speed, improved accuracy, and enhanced safety.
Increased speed: Robots can perform repetitive tasks at a much faster rate than humans, resulting in higher production rates and shorter cycle times.
Improved accuracy: With their precise movements and sensors, robots can consistently perform tasks with minimal errors, reducing waste and improving product quality.
Enhanced safety: By taking over hazardous or physically demanding tasks, robots help create a safer work environment for human workers, reducing the risk of accidents and injuries.
As manufacturing processes become more automated and streamlined with the integration of industrial robots, companies experience increased freedom to focus on innovation and growth while delivering high-quality products efficiently.
Reduce Human Error
One of the key advantages of implementing advanced automation systems in production lines is the significant reduction in human error. Industrial robots, with their precise programming and unparalleled accuracy, can perform repetitive tasks flawlessly, minimizing the risk of mistakes caused by human oversight or fatigue. By eliminating human error from manufacturing processes, companies can ensure consistent quality and reliability in their products.
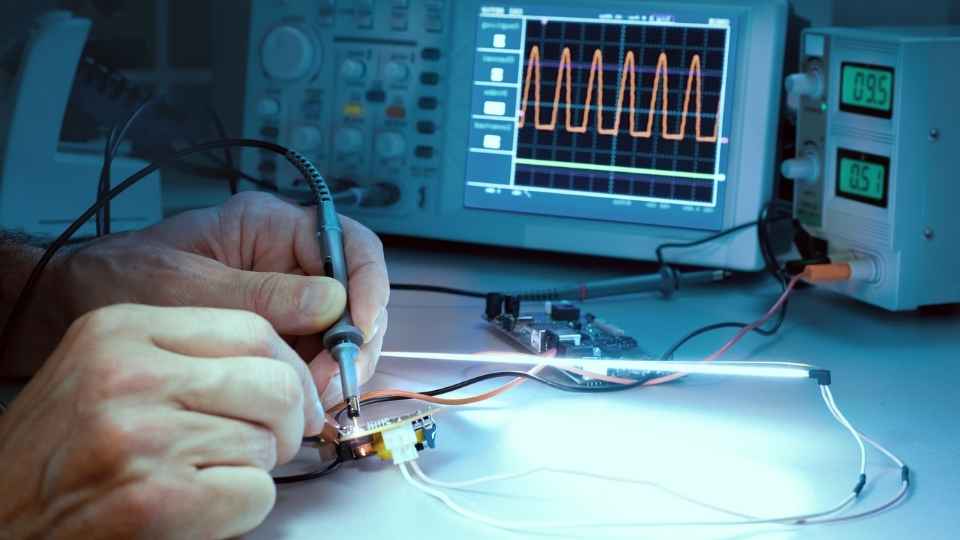
The use of robots in manufacturing also allows for increased freedom for workers. With robots taking over mundane and repetitive tasks, employees are liberated to focus on more complex and creative aspects of their jobs. This not only enhances job satisfaction but also enables workers to develop new skills and take on higher-value responsibilities within the organization.
Moreover, reducing human error through automation leads to improved safety conditions in the workplace. Robots are designed to operate within strict safety parameters, minimizing accidents and injuries that may occur due to human mistakes or negligence.
Increase Output Speed
By implementing advanced automation systems, organizations can experience a significant increase in output speed, allowing for higher production rates and faster delivery of products to meet customer demands. This enhanced efficiency is made possible through the utilization of industrial robots that are capable of performing repetitive tasks with great precision and speed.
Here are three compelling reasons why an audience desiring freedom would be emotionally moved by this development:
Increased productivity: Industrial robots work tirelessly without breaks or fatigue, ensuring round-the-clock operations. This results in a higher volume of goods produced within a given timeframe.
Streamlined processes: Automation eliminates human errors and variability, leading to consistent product quality and reduced waste. This not only improves customer satisfaction but also enhances brand reputation.
Enhanced job satisfaction: By automating mundane and repetitive tasks, organizations free up their workforce to focus on more challenging and creative work, fostering employee growth and job enrichment.
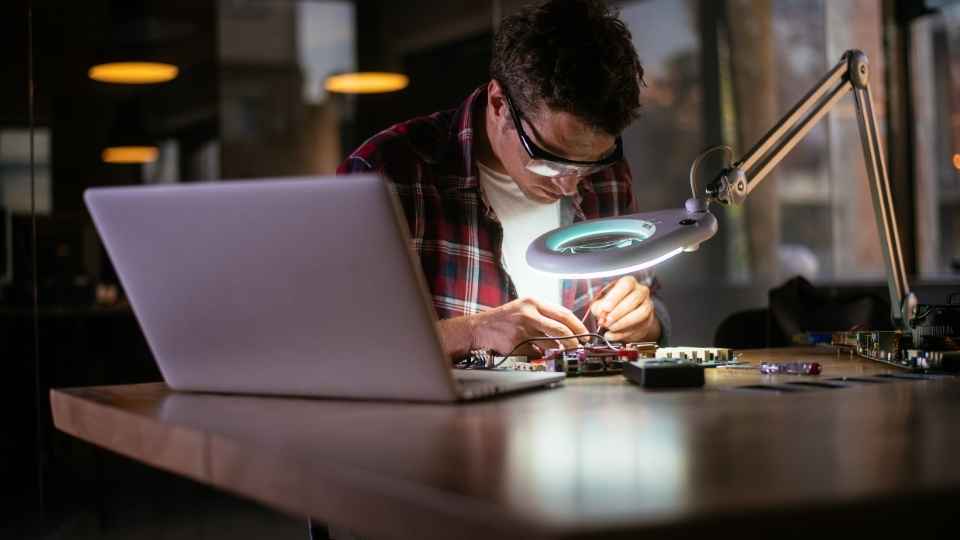
The Impact of Robots on Job Roles and Skills
Robots' influence on job roles and skills in modern manufacturing processes is becoming increasingly evident. As automation technology continues to advance, robots are taking on more complex tasks previously performed by humans. This shift has significant implications for the workforce, as job roles are redefined and new skill sets become necessary.
With the introduction of robots, repetitive and mundane tasks can be automated, freeing up human workers to focus on more creative and higher-value activities. However, this also means that certain job roles may become obsolete or require reskilling to adapt to the changing landscape.
The implementation of robotics in manufacturing necessitates a shift towards a more technical and analytical mindset among workers. Skills such as programming, troubleshooting robotic systems, and data analysis are becoming increasingly valuable in this evolving industry.
Transitioning into the subsequent section about implementing robotics in various industries, it is essential for organizations to identify areas where robots can augment human capabilities effectively while ensuring adequate training programs are in place to equip workers with the skills needed to thrive in this new era of manufacturing.
Implementing Robotics in Various Industries
The integration of automation technology in diverse industries is revolutionizing operational processes and creating new opportunities for increased efficiency and productivity. Implementing robotics has become a game-changer in various sectors, enabling businesses to streamline their operations and achieve higher levels of output.
Here are three ways in which robots are reshaping modern manufacturing processes:
Enhanced safety: By taking over dangerous or repetitive tasks, robots reduce the risk of accidents and injuries for human workers, ensuring a safer working environment.
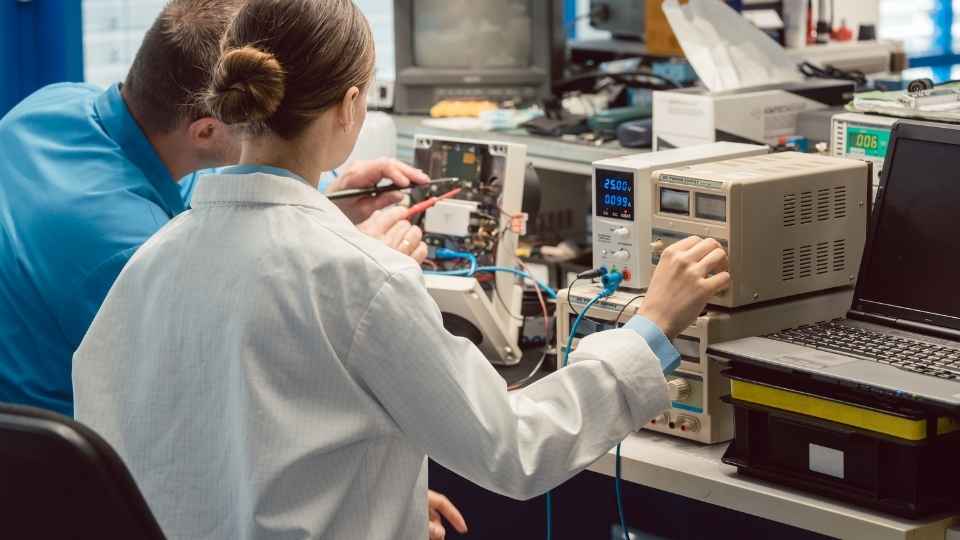
Improved precision: With their precise movements and accuracy, robots can perform intricate tasks with minimal errors, leading to improved product quality and customer satisfaction.
Increased productivity: Robots can work continuously without breaks or fatigue, significantly boosting production rates and allowing companies to meet growing demands efficiently.
As industries embrace automation technology, they not only witness improved operational efficiency but also offer their employees the freedom to focus on more complex and creative aspects of their work.
Future Trends and Challenges in Industrial Robotics
As the field of automation advances, it is crucial for industries to stay updated on emerging trends and overcome challenges in order to fully harness the potential of robotics for their operational processes.
The future of industrial robotics holds several exciting possibilities. One prominent trend is the integration of artificial intelligence (AI) with robots, enabling them to make autonomous decisions and adapt to dynamic environments. This will enhance their versatility and efficiency in performing complex tasks.
Additionally, collaborative robots, or cobots, are gaining popularity as they can work alongside humans safely and efficiently, increasing productivity on the shop floor.
However, these advancements also pose challenges such as ensuring data security and privacy, addressing ethical concerns related to AI-powered robots, and upskilling workers to collaborate effectively with robots.
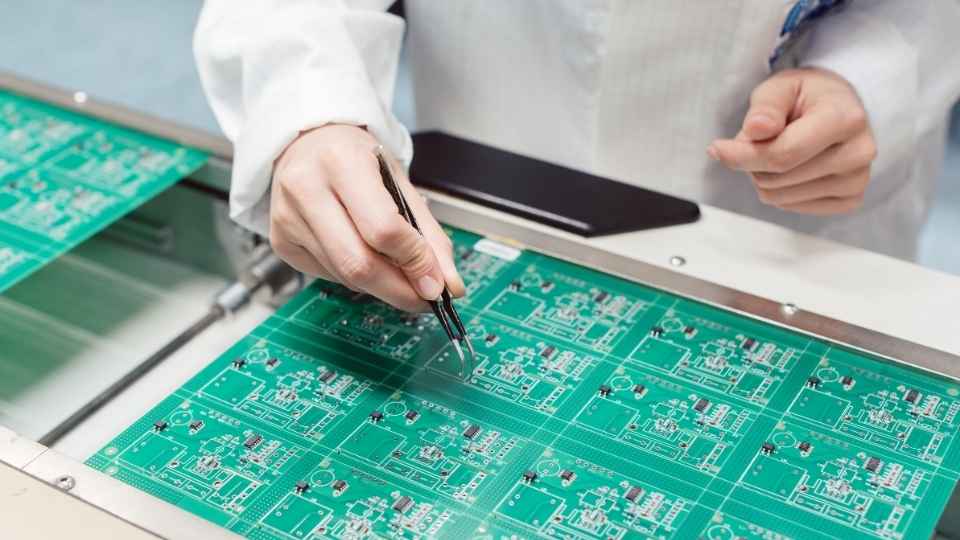
Industries need to proactively address these challenges while embracing the freedom that automation brings.
Frequently Asked Questions
How Do Industrial Robots Affect Workplace Safety in Manufacturing Processes?
Industrial robots have a significant impact on workplace safety in manufacturing processes. They reduce the need for human involvement in hazardous tasks, minimize the risk of accidents, and ensure consistent adherence to safety protocols through their precise and controlled operations.
What Are the Potential Drawbacks or Limitations of Using Robotic Arms and Automation in Manufacturing?
Potential drawbacks and limitations of using robotic arms and automation in manufacturing include high initial costs, the need for skilled technicians to operate and maintain the robots, limited flexibility compared to human workers, and concerns about job displacement.
How Do Robots Impact the Quality Control of Products in the Manufacturing Industry?
Robots greatly impact the quality control of products in the manufacturing industry. They enhance accuracy, consistency, and efficiency by performing precise measurements, detecting defects, and conducting automated inspections, leading to improved product quality and reduced errors.
Are There Any Ethical Concerns Associated With the Use of Robots in Manufacturing?
Ethical concerns associated with the use of robots in manufacturing include potential job displacement, lack of human oversight and control, safety hazards, and privacy issues. These concerns need to be addressed for responsible and sustainable implementation of robotics in the industry.
How Does the Implementation of Robotics in Various Industries Vary, and What Are the Factors That Influence This Variation?
The implementation of robotics varies across industries due to factors such as the complexity of tasks, cost-effectiveness, and compatibility with existing processes. These factors influence the decision-making process for adopting robotic systems in industrial settings.