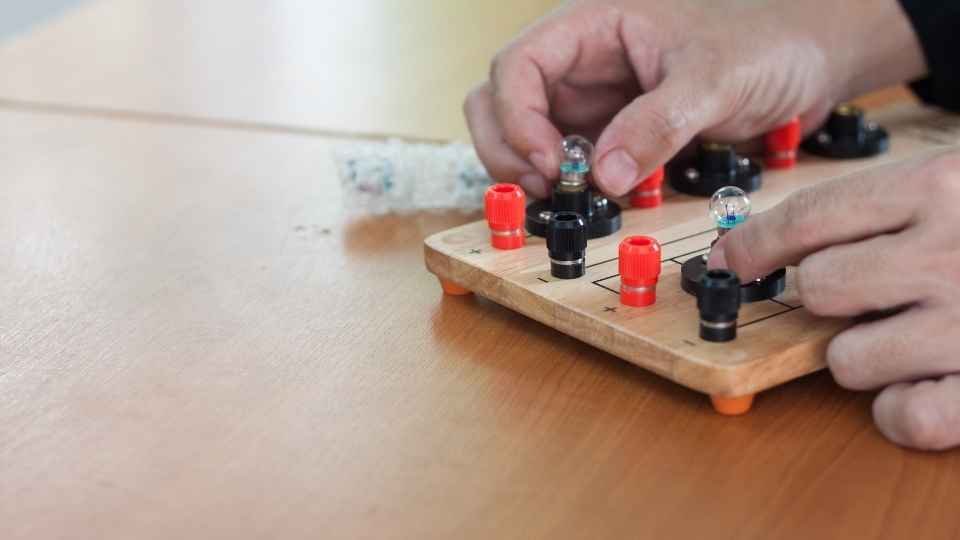
As a passionate soldering enthusiast, I've always believed that the art of soldering goes beyond mere technique. It's about embracing the freedom to create and connect, from flux to lead-free techniques.
In this article, we will delve into the intricate world of soldering, exploring the role of flux, different solder wire choices, essential tooling for soldering irons, mastering desoldering practices, and understanding the shift to lead-free soldering.
Along with tips and tricks for efficient soldering and troubleshooting common issues, get ready to unlock your full potential in the captivating realm of soldering.
Key Takeaways
- Flux is essential for proper adhesion and removal of oxidation during soldering.
- Lead-free soldering is important for environmental protection and worker safety.
- Desoldering techniques allow for repair and component replacement.
- Advanced soldering techniques, such as SMT and wave soldering, cater to specific needs in circuit board production.
The Role of Flux in Soldering Techniques
Flux plays a vital role in soldering by removing oxidation and ensuring proper adhesion. It's a chemical compound that cleans the surfaces to be soldered, allowing for a strong and reliable bond.
The presence of oxidation on metal surfaces can hinder the flow of solder, leading to weak connections or even complete failure. Flux acts as a cleaning agent, dissolving the oxide layer and exposing clean metal underneath. This allows for better heat transfer and improved wetting of the solder onto the surface.
Additionally, flux also prevents re-oxidation during the soldering process by creating a protective barrier on the exposed metal. This ensures that the joint remains stable over time, providing long-lasting connections that are resistant to corrosion or mechanical stress.
Exploring Different Solder Wire Choices
When choosing solder wire, it's important to consider the various options available. Here are three key factors to keep in mind:
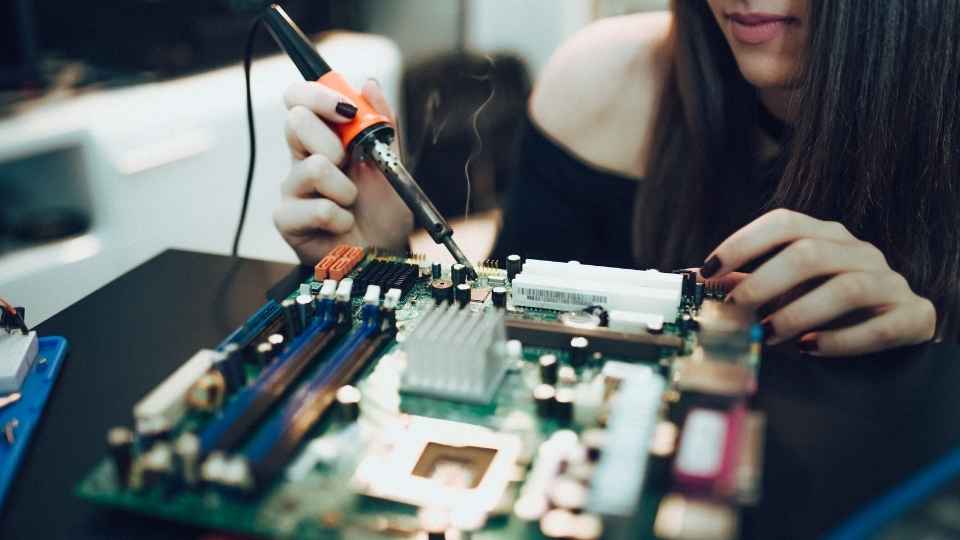
Lead-free options: Opting for lead-free solder wire not only protects your health but also contributes to a safer environment by reducing the impact of hazardous materials on ecosystems.
Flux core content: The flux core in solder wire helps clean and remove oxidation from metal surfaces, ensuring a strong bond. Different flux core formulations cater to specific applications like electronics or plumbing, so choose one that suits your needs.
Wire diameter: The diameter of the solder wire affects how easily it flows and melts during soldering. Thinner wires work well for intricate electronic components, while thicker wires offer better heat transfer for larger joints.
To ensure a successful soldering experience, it's important for you to invest in essential tooling for your soldering iron. These tools won't only enhance your efficiency but also improve the quality of your work.
First and foremost, a good soldering iron stand is crucial to provide a safe and stable place to rest your hot iron when not in use.
Additionally, investing in a high-quality soldering iron tip cleaner will help keep your tip clean and free from oxidation, ensuring optimal heat transfer.
A reliable pair of wire cutters and strippers are essential for preparing wires before soldering.
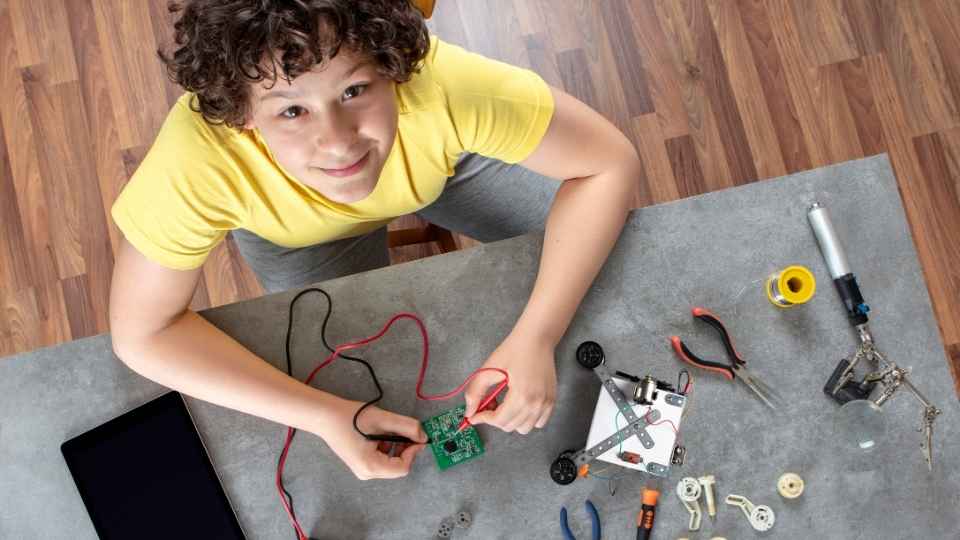
Lastly, don't forget about safety! A heat-resistant mat or pad can protect your work surface from damage while providing insulation against accidental burns.
Mastering Desoldering Practices
You can improve your soldering skills by mastering desoldering practices, which involve removing unwanted solder from joints and components. Desoldering is a crucial skill for any electronics enthusiast or professional, as it allows for the repair and replacement of faulty components.
Here are three reasons why mastering desoldering practices is essential:
Precision: Proper desoldering techniques ensure that you can remove excess solder without damaging surrounding components or circuitry, leading to cleaner and more efficient repairs.
Efficiency: By efficiently removing unwanted solder, you save time and effort during rework or component replacement processes.
Versatility: Desoldering skills enable you to salvage valuable components from old or broken devices, promoting sustainability and cost-effectiveness.
By becoming proficient in desoldering techniques, you'll have the freedom to work on a wider range of projects with confidence.
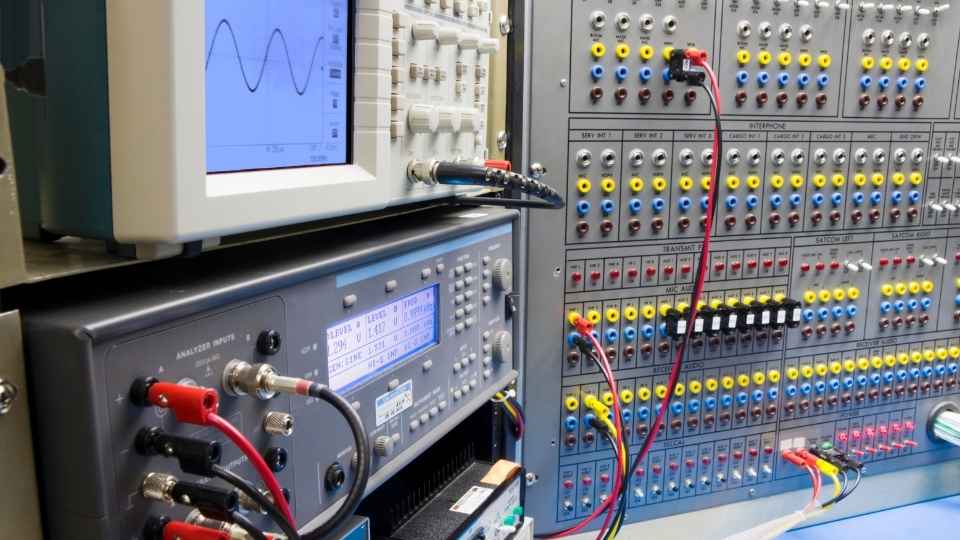
Now let's delve into understanding the shift to lead-free soldering methods.
Understanding the Shift to Lead-Free Soldering
Understanding the shift to lead-free soldering is crucial in today's electronics industry. With increasing environmental concerns and regulatory requirements, the use of lead-based solder has been phased out in many applications.
This transition aims to minimize the harmful effects of lead on human health and the environment, while still maintaining high-quality connections and reliability in electronic assemblies.
Benefits of Lead-Free Soldering
Switching to lead-free soldering has numerous advantages, such as reducing environmental pollution and improving worker safety. Here are three compelling reasons why embracing this technique is crucial for those seeking freedom:
Healthier Planet: Lead-free soldering significantly reduces the release of toxic substances into the environment, safeguarding ecosystems and preserving natural resources. By choosing this method, we contribute to a cleaner and greener world.
Safer Working Conditions: Lead-based solder emits hazardous fumes during the soldering process, posing health risks to workers. With lead-free alternatives, we prioritize the well-being of individuals by eliminating exposure to harmful chemicals in their workplace.
Compliance with Regulations: Many countries have implemented strict regulations regarding the use of lead in manufacturing processes. Embracing lead-free soldering ensures compliance with these regulations while staying ahead of industry standards.
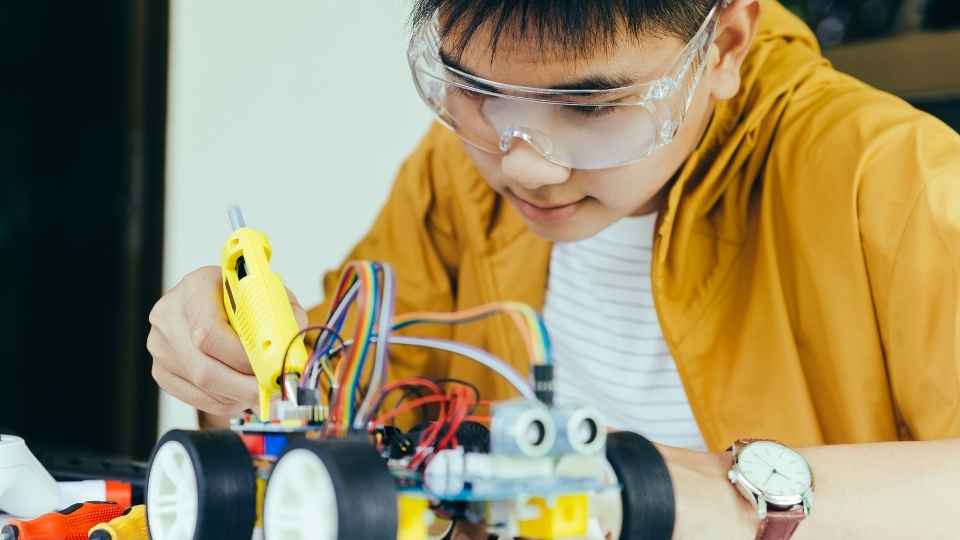
Challenges of Lead-Free Soldering
Now let's delve into the challenges of lead-free soldering. As a soldering enthusiast, I've encountered various obstacles when working with lead-free solder.
One major challenge is the higher melting temperature of lead-free alloys compared to traditional lead-based ones. This requires careful adjustment of the soldering iron temperature and technique to ensure proper bonding without damaging sensitive components.
Another hurdle is the increased occurrence of tin whiskers in lead-free solder joints. These tiny, hair-like structures can grow over time and cause short circuits or other reliability issues. To mitigate this problem, manufacturers employ various methods such as alloy additions and conformal coatings.
Furthermore, the reduced wetting ability of lead-free solder can pose difficulties in achieving good joint formation, especially on certain surfaces like copper. Proper flux selection and application techniques are crucial to ensure adequate wetting and reliable connections.
Despite these challenges, advancements in materials and techniques continue to improve the performance and reliability of lead-free soldering processes.
Tips and Tricks for Efficient Soldering
As an experienced soldering technician, I've honed my skills and developed some valuable tips and tricks for efficient soldering.
By mastering heat management techniques, such as preheating the components and using the appropriate soldering iron temperature, you can ensure precise and reliable connections.
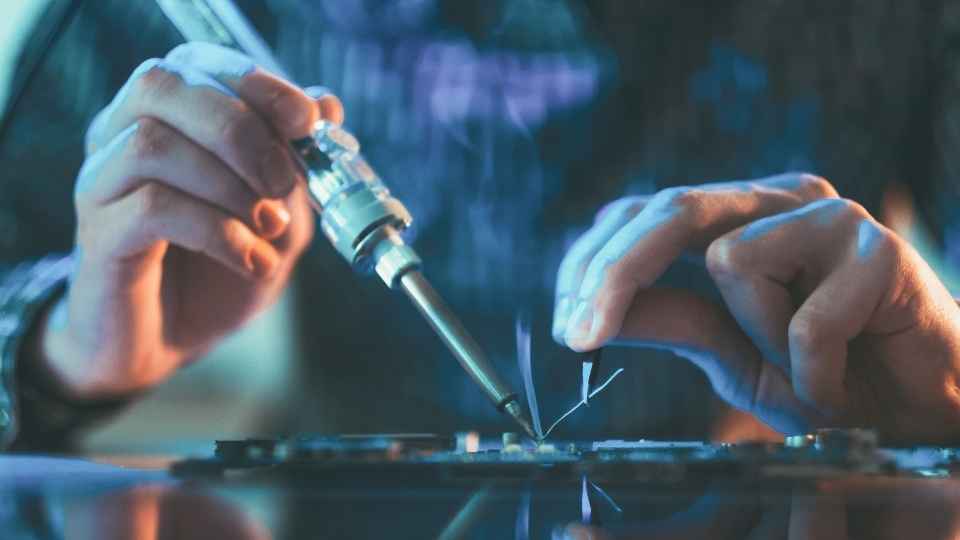
Additionally, selecting the right type of solder for your specific application is crucial in achieving optimal results.
Heat Management Techniques
One effective way to manage heat during soldering is by using heat sinks. Heat sinks are devices that absorb and dissipate heat generated by the soldering process, preventing damage to delicate components and ensuring a successful solder joint.
Here are three reasons why heat sinks are essential for efficient and safe soldering:
Enhanced Thermal Management: Heat sinks provide an additional surface area for heat transfer, allowing excess heat to disperse quickly. This prevents overheating of components and reduces the risk of thermal damage.
Improved Solder Joint Quality: By minimizing temperature fluctuations, heat sinks help maintain a stable working environment for soldering. This results in stronger, more reliable solder joints with reduced chances of cold joints or other defects.
Increased Worker Comfort: Soldering can generate significant amounts of heat, making it uncomfortable to handle certain components or work for extended periods. Heat sinks help regulate temperatures, creating a more comfortable environment for the operator.
With proper heat management using heat sinks, you can now move on to selecting the right type of solder for your project.
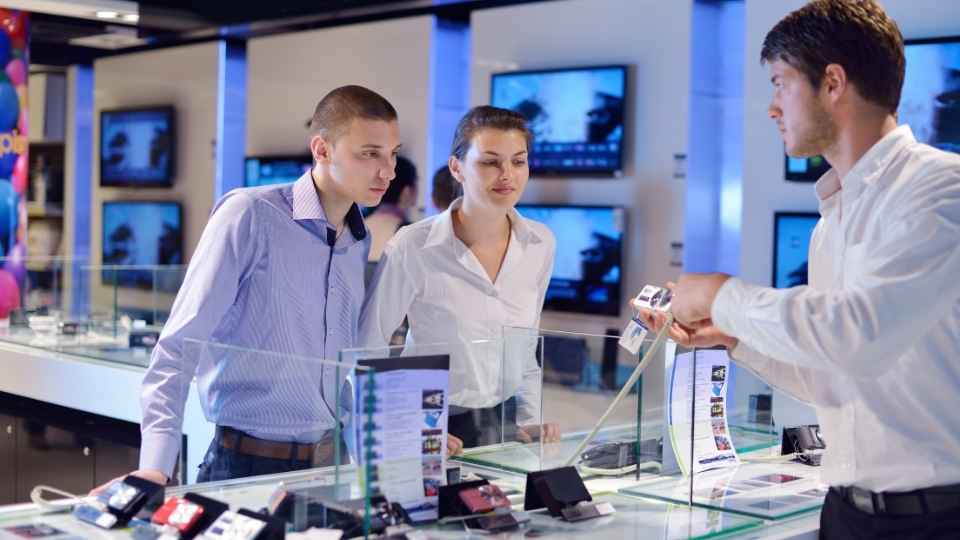
Choosing the Right Solder
To choose the right solder for your project, you'll need to consider factors such as melting point, composition, and flux core.
The melting point is crucial because it determines the temperature at which the solder will become liquid and bond with the materials being joined. Different projects require different temperatures, so it's important to select a solder with a melting point that suits your needs.
Composition refers to the metals present in the solder alloy. Common compositions include tin-lead (Sn-Pb) and lead-free alloys like tin-silver-copper (SAC). Consider your application requirements and any regulatory restrictions when choosing a composition.
Lastly, flux core plays an essential role in soldering by removing oxides from metal surfaces and promoting proper wetting. Choose a flux core that matches your project's needs, whether it be rosin-based or water-soluble.
Troubleshooting Common Soldering Issues
If you're experiencing common soldering issues, such as poor joint connections or excessive heat, try adjusting your technique and equipment. Here are three tips to help troubleshoot these problems:
Check your soldering iron temperature: Make sure you're using the correct temperature for the type of solder and components you're working with. Adjust the temperature accordingly to avoid overheating or underheating.
Improve your soldering technique: Ensure that you've a clean and properly tinned tip on your soldering iron. Use flux to promote better wetting and flow of solder onto the joint. Practice steady hand movements and apply just enough heat to create a good bond without causing damage.
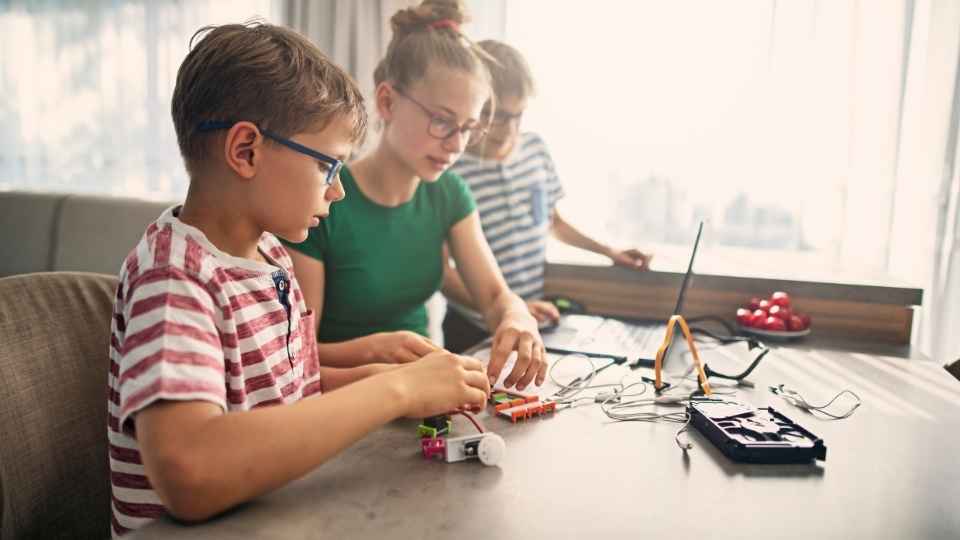
Inspect your materials: Examine your solder wire, flux, and components for any signs of contamination or defects. Using high-quality materials can significantly reduce common soldering issues.
Frequently Asked Questions
What Are Some Common Safety Precautions to Take While Soldering?
When soldering, it's important to prioritize safety. Some common precautions include wearing protective eyewear, using a well-ventilated area or fume extractor, and avoiding contact with hot surfaces or molten solder.
Can You Provide a Step-By-Step Guide on How to Clean a Soldering Iron Tip?
Sure, I can provide a step-by-step guide on how to clean a soldering iron tip. It's important to keep the tip clean for proper soldering. Here's what you need to do.
How Do I Prevent Solder Joints From Cracking or Breaking?
To prevent solder joints from cracking or breaking, I ensure proper preparation by cleaning the surfaces to be joined and using the correct soldering temperature. Additionally, I make sure to provide adequate support for the joint during cooling.
What Is the Difference Between Lead-Free Solder and Traditional Solder?
Lead-free solder is a newer alternative to traditional solder, containing no lead. It offers environmental benefits but requires higher temperatures for melting and may have different mechanical properties.
Are There Any Specific Techniques for Soldering Delicate or Small Components?
When soldering delicate or small components, it's important to use precision techniques. Make sure to handle the components with care and apply just the right amount of heat. Practice makes perfect!