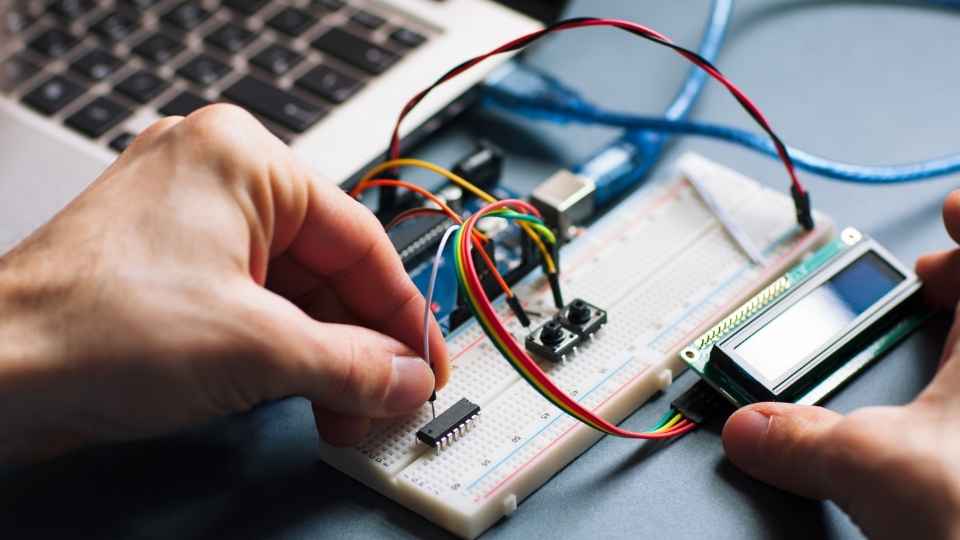
In the increasingly digital world we live in, the concept of robotics has become an integral part of our daily lives. From automated vacuum cleaners to self-driving cars, the possibilities seem limitless.
For those who have always been fascinated by the world of robots but are unsure where to start, this article aims to serve as a comprehensive guide. We will delve into the mechanics behind DIY robots, explore coding for beginners, and provide troubleshooting tips for aspiring robot builders.
Join us on this exciting journey as we unlock the secrets of easy DIY robots from mechanics to movement.
Key Takeaways
- Consider level of expertise and desired learning outcomes when choosing a beginner kit
- Incorporate simple sensors to enhance robot capabilities
- Familiarize with basic programming languages like Python or Arduino
- Thorough understanding of sensor technology and robotic mechanics is necessary
Choosing the Right Beginner Kit
When it comes to starting your journey in building DIY robots, it is crucial to carefully consider and choose the right beginner kit that suits your level of expertise and desired learning outcomes.
A good beginner kit will provide you with the necessary components and instructions to understand the basic principles of robotics while allowing room for creativity and freedom in design. Look for kits that include a microcontroller board, motors, sensors, and various mechanical parts such as wheels or arms.
These kits should also come with detailed documentation, tutorials, and sample projects to guide you through the learning process. Additionally, consider whether you want a kit that focuses more on mechanics or programming, depending on your interests and goals.
Understanding the Basics of Robot Mechanics
Understanding the basics of robot mechanics is crucial for designing and building efficient and functional robotic systems.
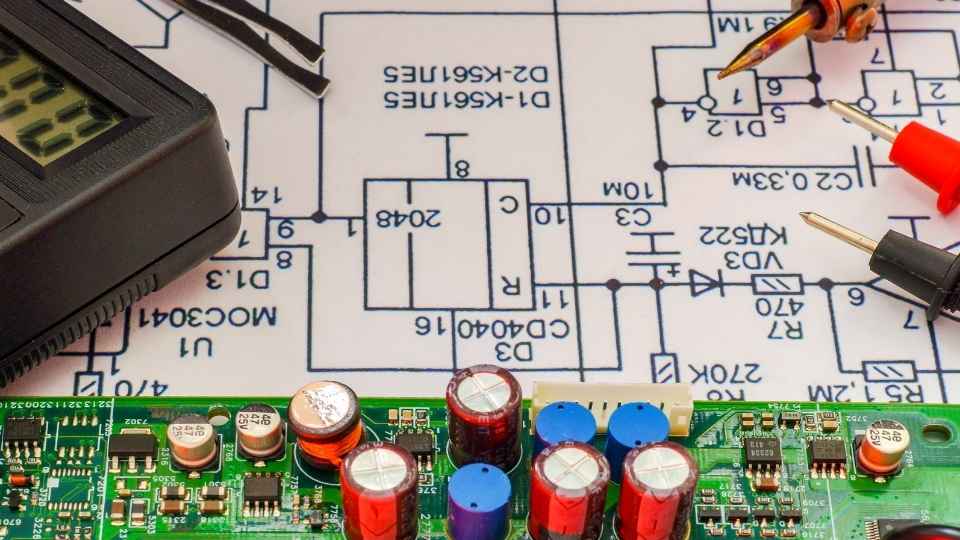
It involves a deep understanding of the robot body structure, mechanical joints, actuators, power systems, and propulsion methods.
Robot Body Structure
The robot body structure plays a crucial role in determining the overall stability and functionality of the DIY robot. A well-designed and sturdy body ensures that the robot can withstand external forces and perform its intended tasks effectively.
Here are five key factors to consider when designing the robot's body structure:
Material: Choosing the right materials such as lightweight metals or durable plastics is essential for balancing weight, strength, and cost.
Joints: Proper joint selection and placement allow for smooth movement and flexibility of the robot's limbs or appendages.
Center of Gravity: Positioning the center of gravity correctly ensures stability during motion and prevents toppling over.
Enclosures: Protective enclosures shield sensitive components from environmental factors while providing easy access for maintenance.
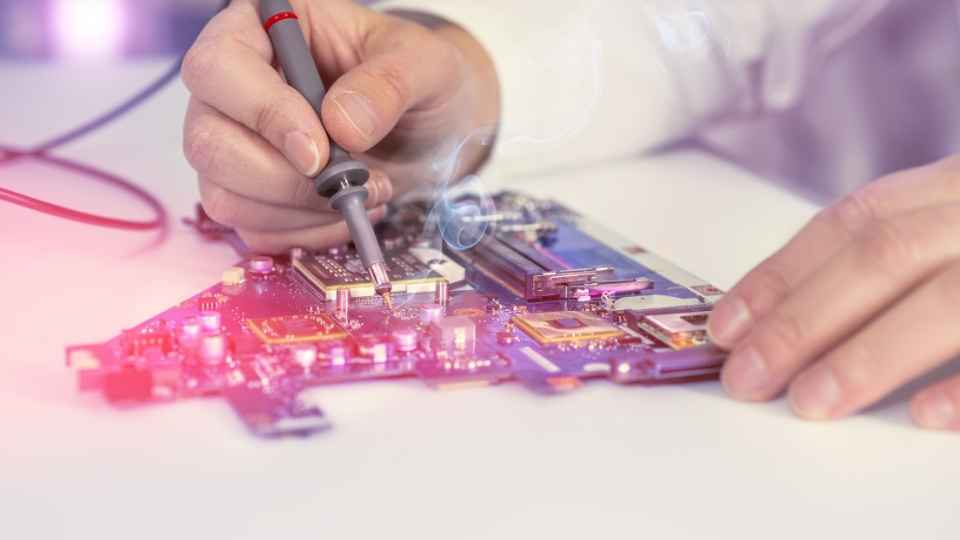
Modularity: A modular design allows for easy customization, repair, or upgrading of individual components without affecting the entire system.
Mechanical Joints and Actuators
Proper selection and placement of mechanical joints and actuators are critical for achieving smooth and precise movement in the robot's limbs or appendages. Mechanical joints provide flexibility and allow for rotational or linear motion, while actuators convert energy into motion.
The choice of joint type depends on the desired range of motion, load-bearing capacity, and stability requirements. Common types include revolute (hinge), prismatic (slider), spherical (ball-and-socket), and planar (sliding) joints.
Actuators can be hydraulic, pneumatic, or electrically powered, each with its own advantages and limitations. Hydraulic actuators offer high force capabilities but require a power source. Pneumatic actuators are lightweight but may have limited precision. Electric actuators are versatile with precise control but have lower force capabilities compared to hydraulics.
Successful integration of these components ensures efficient movement in robots' limbs or appendages, allowing them to perform tasks effectively while maintaining freedom of movement.
Power and Propulsion Systems
Efficient power and propulsion systems are crucial for the successful operation of robots, as they provide the necessary energy and drive to enable smooth locomotion and maneuverability. To achieve optimal performance, several factors need to be considered when designing these systems:
Power Source: Selecting the appropriate power source is vital. This could include batteries, fuel cells, or even renewable energy options like solar panels.
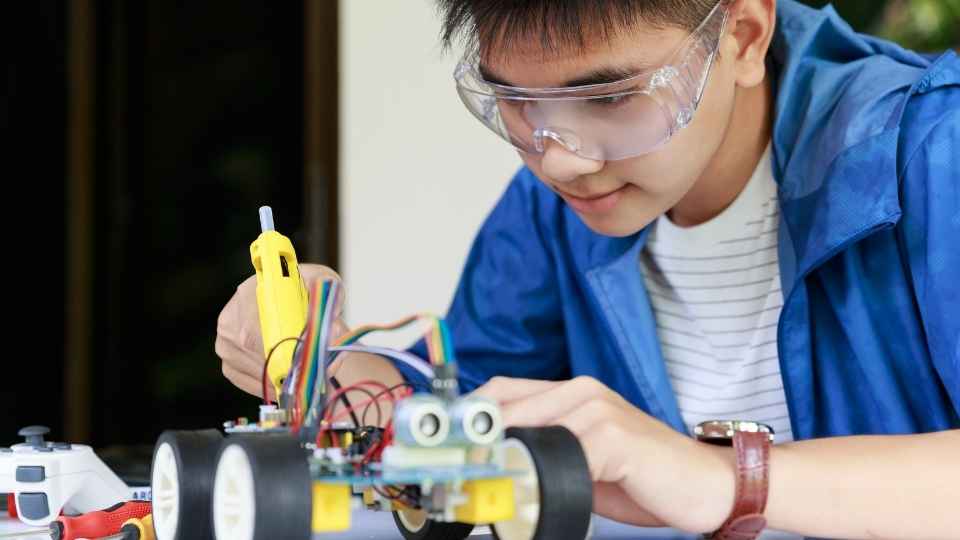
Energy Conversion: Efficiently converting stored energy into mechanical motion is essential. This can be achieved using motors, actuators, or other mechanisms.
Transmission Systems: The transmission of power from the source to the actuators should minimize losses and ensure maximum efficiency.
Control Systems: Implementing control algorithms that regulate power delivery and optimize propulsion efficiency is crucial.
Redundancy: Incorporating redundancy in power and propulsion systems enhances reliability by providing backup options in case of failures.
Designing efficient power and propulsion systems requires careful consideration of these factors to ensure optimal performance, longer operational times, and greater freedom in robot movements.
Exploring Simple Sensors for DIY Robots
As we delve further into the realm of DIY robots, it becomes evident that incorporating simple sensors is essential for enhancing their capabilities. Simple sensors play a critical role in enabling robots to perceive and interact with their environment.
In this section, we will explore different types of sensors, their functions, how they can be integrated with robot mechanics, and troubleshooting common sensor issues.
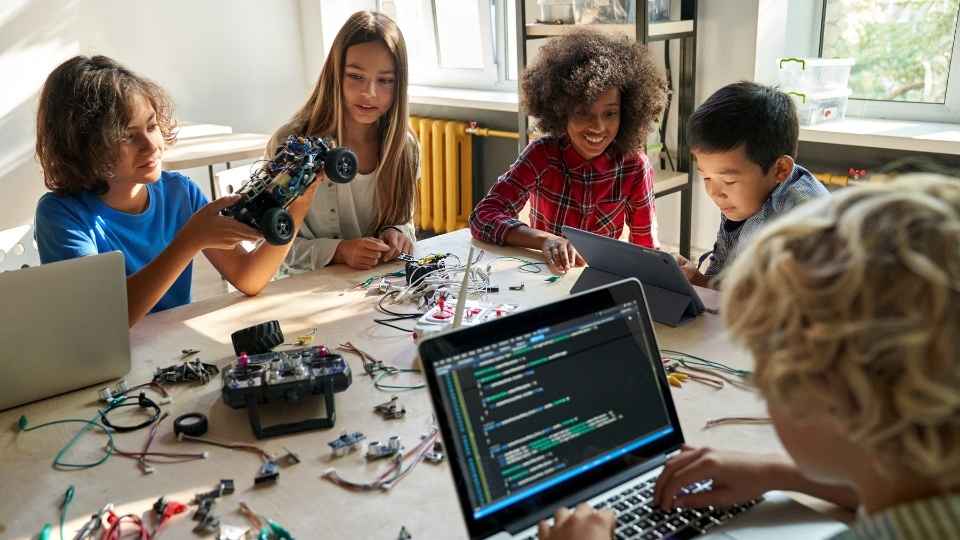
Sensor Types and Functions
Different sensor types serve various functions in robotics, allowing for the detection and measurement of specific environmental factors. These sensors play a crucial role in enabling robots to interact with their surroundings and make informed decisions.
Some common sensor types used in robotics include:
- Proximity Sensors: Used to detect the presence or absence of objects within a certain range.
- Temperature Sensors: Measure the ambient temperature and provide feedback for temperature regulation or thermal monitoring.
- Light Sensors: Detect variations in light intensity, enabling robots to adapt their behavior based on changes in lighting conditions.
- Force Sensors: Measure the force exerted by an object, helping robots handle delicate objects or apply controlled force when necessary.
- Infrared Sensors: Enable robots to detect infrared radiation, allowing them to navigate and avoid obstacles even in low-light environments.
Integration With Robot Mechanics
The successful integration of sensors with the mechanical components of a robot is essential for seamless operation and accurate perception of the surrounding environment. Sensors provide vital feedback to the robot's control system, enabling it to make informed decisions and respond appropriately to its surroundings.
To achieve optimal integration, careful consideration must be given to the placement and orientation of sensors within the robot's structure. Factors such as sensor range, resolution, and response time need to be taken into account when selecting and positioning sensors.
Additionally, proper calibration and synchronization between the sensors and mechanical components are crucial for accurate data acquisition and interpretation. The integration process requires a thorough understanding of both sensor technology and robotic mechanics, as well as expertise in programming algorithms that enable effective sensor fusion.
Troubleshooting Sensor Issues
To effectively troubleshoot sensor issues, it is important to have a comprehensive understanding of the sensor technology and its interaction with the robot's control system. Sensors play a critical role in providing robots with the ability to perceive their environment.
Here are five key factors to consider when troubleshooting sensor issues:
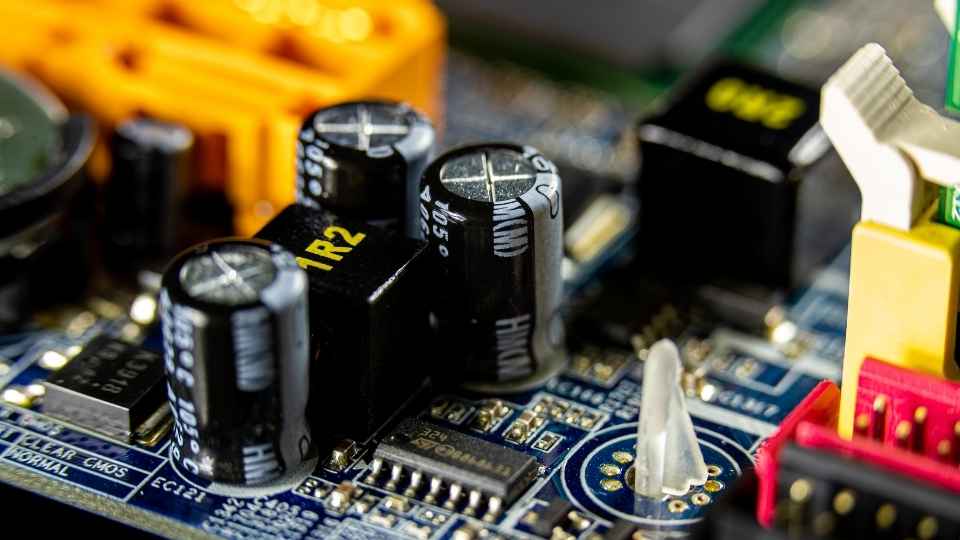
Check the physical connections: Ensure that all cables and connectors are securely connected and not damaged.
Verify power supply: Confirm that the sensor is receiving adequate power supply as per its specifications.
Calibrate the sensor: Perform calibration procedures to ensure accurate readings from the sensor.
Test in different environments: Assess if the issue persists across various environments, as certain conditions may affect sensor performance.
Update firmware or software: Check for any available updates for both the control system and sensor firmware.
By following these troubleshooting steps, you can effectively address any sensor-related issues and enhance your robot's functionality.
Now let's move on to getting started with coding for beginners.
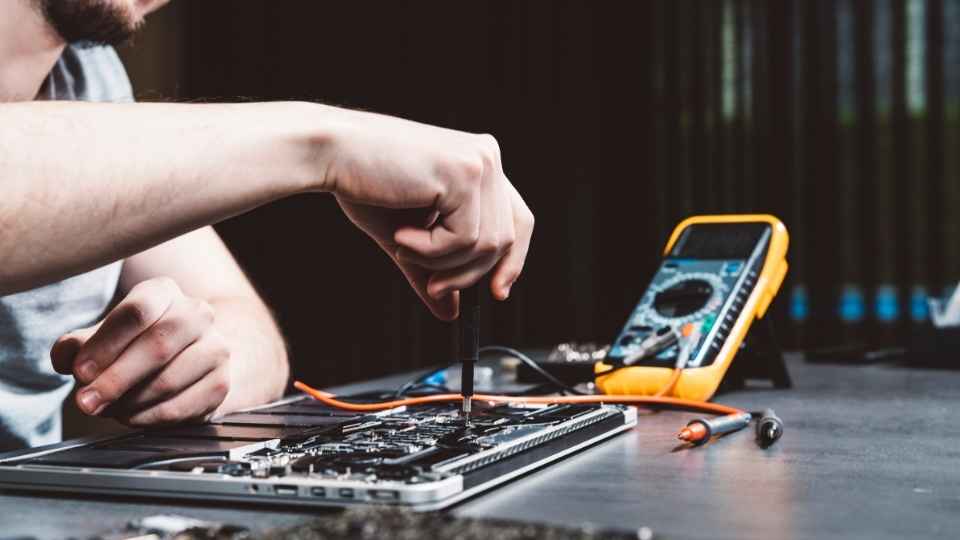
Getting Started With Coding for Beginners
When beginning your journey into coding for robotics, it is essential to familiarize yourself with basic programming languages such as Python or Arduino. These languages provide a solid foundation for understanding the logic and syntax of coding, enabling you to create programs that control the behavior of your robots.
Python is a versatile language known for its simplicity and readability, making it ideal for beginners. Its extensive libraries and community support also contribute to its popularity among programmers.
Arduino, on the other hand, is an open-source platform specifically designed for electronics projects like robotics. It offers a simplified version of C++ programming language and provides easy integration with hardware components.
Both Python and Arduino allow beginners to quickly grasp the concepts of coding while providing flexibility and freedom in designing robotic systems.
Essential tools and equipment for building robots include a soldering iron, wire cutters, pliers, a multimeter, and a breadboard. These tools are crucial for assembling the mechanical components of the robot and ensuring its proper functioning.
Here is an unordered bullet list of these essential items:
- Soldering Iron: Used to join electrical components together by melting solder onto them.
- Wire Cutters: Necessary for cutting wires to the desired length and stripping insulation.
- Pliers: Useful for gripping small parts, bending wires, and making precise adjustments.
- Multimeter: A versatile tool that measures voltage, current, resistance, and continuity in electrical circuits.
- Breadboard: Allows for prototyping circuits without soldering by providing interconnected contact points.
Having these tools at your disposal will empower you to build robots with ease while exploring your creative freedom.
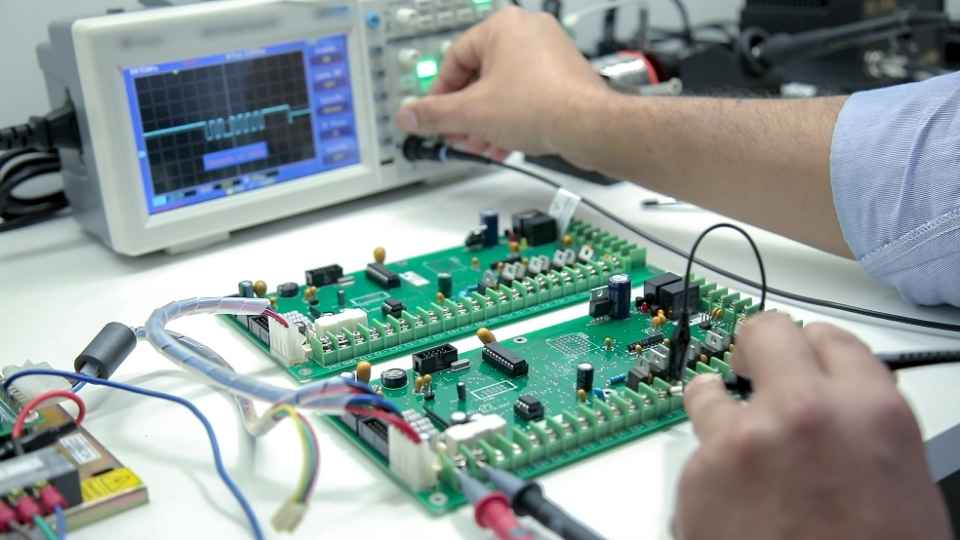
Now let's delve into mastering the art of robot movement.
Mastering the Art of Robot Movement
Now that we have covered the essential tools and equipment for robot building, it is time to delve into the intricate world of mastering the art of robot movement. The ability to control a robot's movement is crucial in achieving desired functionality and efficiency. There are various methods of achieving precise and fluid motion in robots, such as using motors, servos, or pneumatics.
One key aspect to consider when designing robot movement is kinematics. Kinematics involves analyzing the motion of objects without considering their mass or forces involved. By understanding kinematic principles, one can determine how different joints and actuators should be positioned to achieve specific movements.
Additionally, programming plays a vital role in controlling robot movement. Algorithms need to be developed that take inputs from sensors and translate them into appropriate actions for the robot's motors or servos.
Mastering the art of robot movement requires a combination of mechanical design expertise, knowledge of kinematics principles, and proficiency in programming algorithms. With these skills at hand, one can create robots capable of performing intricate tasks with precision and freedom in movement.
Troubleshooting Tips for DIY Robot Builders
To ensure optimal functionality and efficiency, it is important for robot builders to have a thorough understanding of troubleshooting techniques. Troubleshooting is a critical skill that allows builders to identify and resolve issues that may arise during the construction or operation of a DIY robot.
Here are five essential tips for effective troubleshooting:
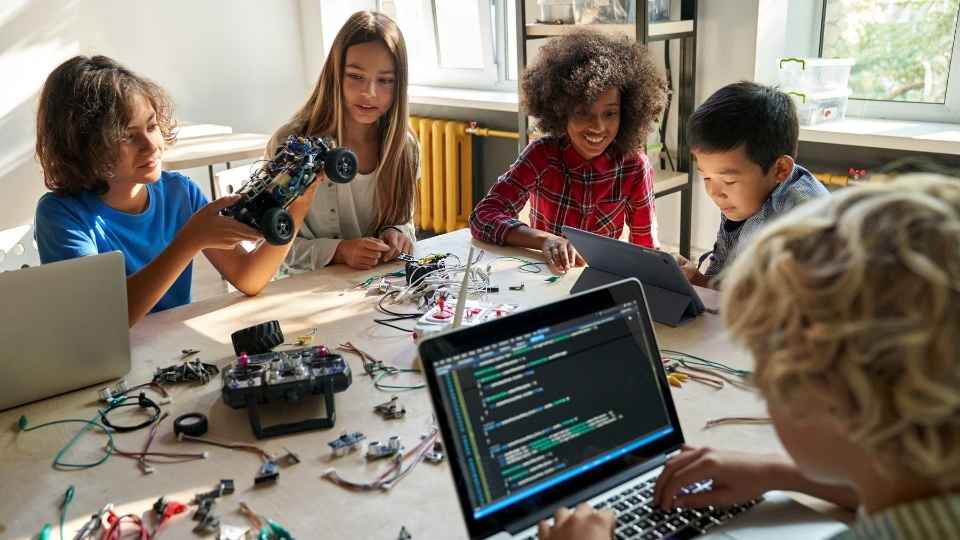
Start with a systematic approach: Break down the problem into smaller components and test each one individually.
Check the power source: Ensure that all batteries are fully charged and properly connected.
Review the code: Verify that the programming logic is correct and check for any syntax errors.
Inspect physical connections: Examine all wires, cables, and connectors to ensure they are securely attached.
Utilize diagnostic tools: Take advantage of multimeters, oscilloscopes, or other testing equipment to measure voltages, currents, and signals.
Frequently Asked Questions
How Much Does a Beginner Robot Kit Typically Cost?
A beginner robot kit typically costs between $50 to $150, depending on the complexity and features included. This price range allows beginners to access a basic set of components and tools needed to build their first DIY robot.
Are There Any Safety Precautions I Should Take When Building a DIY Robot?
When building a DIY robot, it is crucial to prioritize safety precautions. This includes wearing protective gear, working in a well-ventilated area, and ensuring proper insulation of electrical components to prevent any potential hazards or accidents.
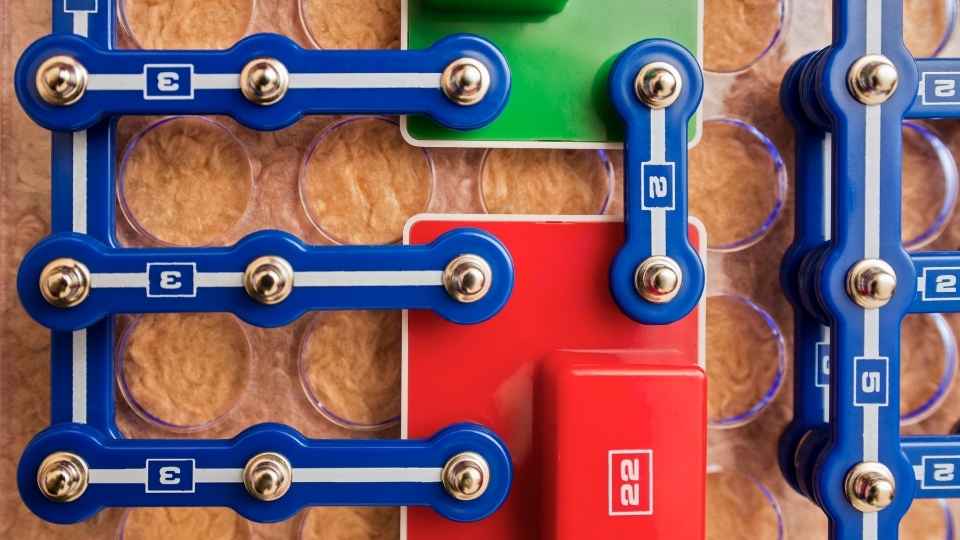
Can I Use Different Coding Languages to Program My DIY Robot?
Yes, different coding languages can be used to program a DIY robot. The choice of language depends on the specific capabilities and requirements of the robot, as well as the programmer's familiarity and preference.
What Are Some Common Mistakes to Avoid When Building a DIY Robot?
When building a DIY robot, it is crucial to avoid common mistakes that can hinder its functionality. Some of these include improper wiring, inadequate power supply, lack of testing and debugging, and neglecting safety precautions.
How Long Does It Usually Take to Build a Basic DIY Robot?
The time it takes to build a basic DIY robot can vary depending on the complexity of the project, the knowledge and experience of the builder, and the availability of resources.