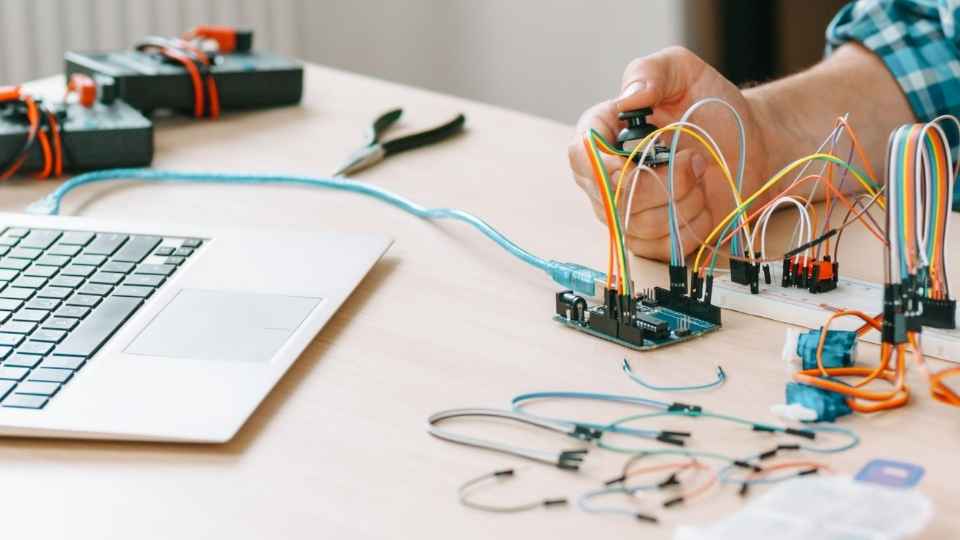
In an ever-evolving electronics industry, ensuring reliability is a paramount concern for manufacturers. With the increasing complexity of electronic devices, quality assurance engineers play a crucial role in guaranteeing that products meet the highest standards.
This article explores the various steps and techniques involved in product validation to ensure electronics reliability. From implementing effective quality control measures to tracking and resolving defects, this comprehensive guide provides insights into best practices for long-term electronics reliability.
By prioritizing thoroughness and precision, quality assurance engineers can confidently deliver products that exceed customer expectations.
Key Takeaways
- Quality assurance is essential in the electronics industry to ensure products meet quality standards, enhance customer satisfaction, and maintain a competitive edge.
- Product validation for electronics reliability involves defining clear requirements, conducting design reviews, rigorous testing, functional tests, and reliability analysis.
- Testing techniques such as functional and non-functional tests help ensure electronics quality, identify issues and defects, and build trust with consumers.
- Reliability analysis plays a crucial role in electronics product development by identifying potential failures, ensuring quality and dependability, and informing design improvements.
Importance of Quality Assurance in Electronics Industry
Quality assurance plays a crucial role in the electronics industry as it ensures that products meet quality standards and reliability requirements, ultimately enhancing customer satisfaction and minimizing potential risks. In an industry driven by technological advancements and fierce competition, maintaining quality is essential to gain an edge over competitors. Electronics manufacturers invest significant resources in quality assurance processes to ensure that their products are free from defects and perform optimally.
The importance of quality assurance lies in its ability to identify and rectify any issues or flaws before the product reaches the market. Through meticulous testing and validation procedures, quality assurance engineers can mitigate potential risks such as malfunctions, safety hazards, or poor performance. This not only safeguards the reputation of the company but also enhances customer trust and loyalty.
Moreover, quality assurance helps companies comply with regulatory standards set by governing bodies. These standards ensure product safety, environmental sustainability, and overall consumer protection. By adhering to these regulations through rigorous quality checks, manufacturers can avoid legal complications and penalties while demonstrating their commitment to responsible business practices.
Key Steps in Product Validation for Electronics Reliability
One crucial aspect in achieving high standards of electronics reliability is the thorough validation process, which involves key steps that ensure the functionality and performance of the product.
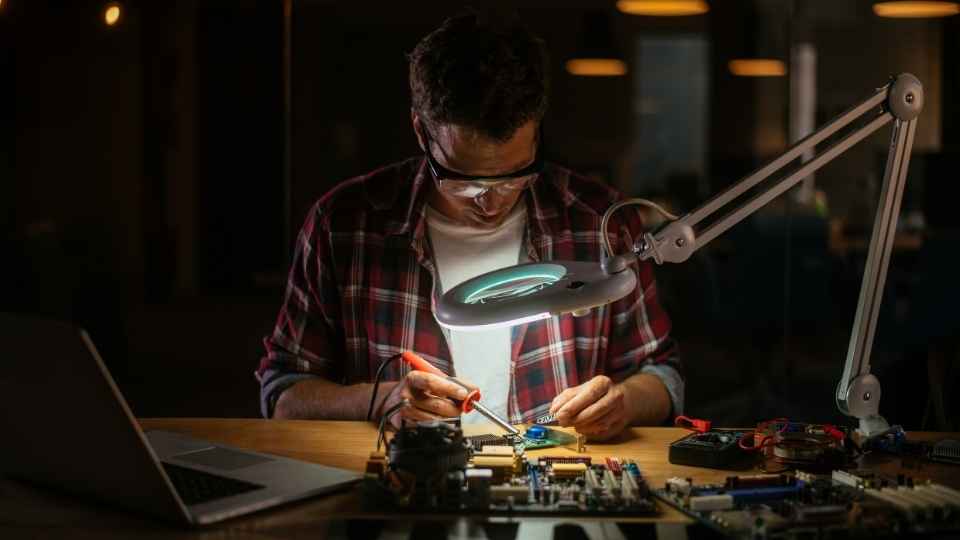
The first step in product validation is defining clear requirements and specifications for the electronic device. This ensures that all stakeholders are aligned on what needs to be achieved.
Next, a comprehensive design review is conducted to identify any potential issues or risks before moving forward with production.
Once the design is finalized, rigorous testing is carried out to verify its performance under various conditions such as temperature, humidity, and voltage fluctuations. Additionally, functional tests are conducted to assess if the device meets all specified requirements.
Finally, a reliability analysis is performed to estimate the expected lifespan of the product and identify any potential areas for improvement.
By following these key steps in product validation, electronics manufacturers can ensure that their products meet high standards of reliability.
Transition: Now that we have discussed the key steps in product validation for electronics reliability, let us explore some testing techniques for ensuring electronics quality.
Testing Techniques for Ensuring Electronics Quality
To ensure the robustness and performance of electronic devices, it is essential to implement a range of testing techniques that assess their functionality and adherence to specifications. These testing techniques include both functional and non-functional tests.
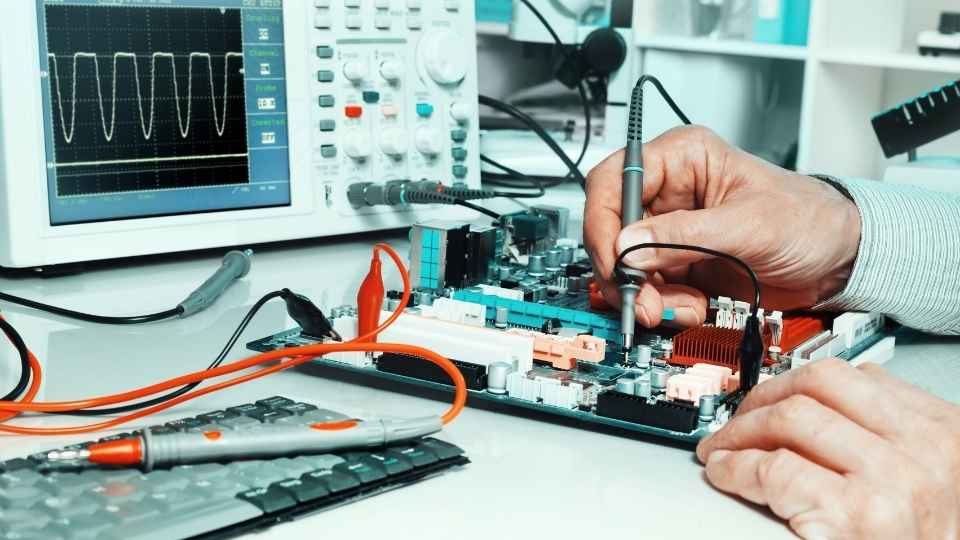
Functional tests evaluate the device's ability to perform its intended tasks, while non-functional tests focus on factors such as reliability, performance, and security.
Functional testing involves validating each feature of the device against predetermined requirements. This can be done through unit testing, integration testing, system testing, and user acceptance testing.
Non-functional tests assess the device's reliability by subjecting it to stress tests, load tests, and performance monitoring.
By conducting thorough and meticulous testing, quality assurance engineers can identify any issues or defects in the electronic devices before they reach the market. This not only ensures customer satisfaction but also helps in building trust with consumers.
In the subsequent section about 'role of reliability analysis in electronics product development', we will explore how reliability analysis plays a crucial role in ensuring the overall quality and longevity of electronic devices.
Role of Reliability Analysis in Electronics Product Development
Reliability analysis is a critical aspect of the development process for electronic devices. It helps identify potential failures and weaknesses that could impact their overall performance and longevity.
By conducting thorough and meticulous reliability analysis, manufacturers can ensure the quality and dependability of their products. This gives consumers the freedom to use them without worry.
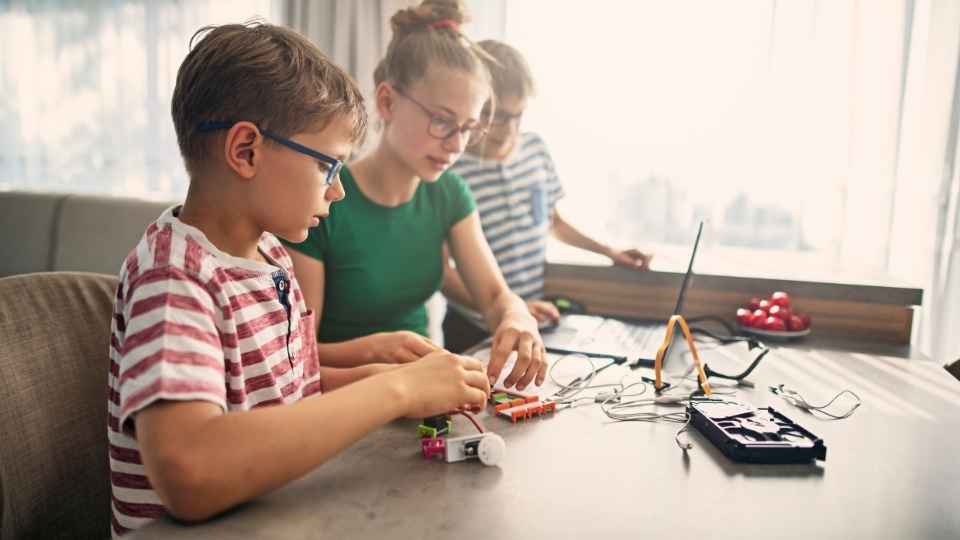
This analysis involves various techniques such as accelerated life testing, environmental stress testing, and failure mode analysis. These methods allow engineers to simulate real-world conditions and assess how different factors like temperature, humidity, vibration, and electrical stress affect the device's reliability.
Through this precise evaluation of potential risks, manufacturers can make informed decisions regarding design improvements or modifications to enhance product durability.
Reliability analysis plays a vital role in ensuring electronics meet high standards of quality and satisfy consumer demands for reliable and long-lasting devices.
Implementing Effective Quality Control Measures in Electronics Manufacturing
Implementing effective quality control measures is essential in the manufacturing of electronics, as it ensures that all components and processes meet stringent standards for performance and durability.
The following measures can be implemented to ensure high-quality electronics:
Regular inspection and testing of raw materials to identify any defects or inconsistencies.
Incorporating automated testing systems to detect faults in electronic components during the manufacturing process.
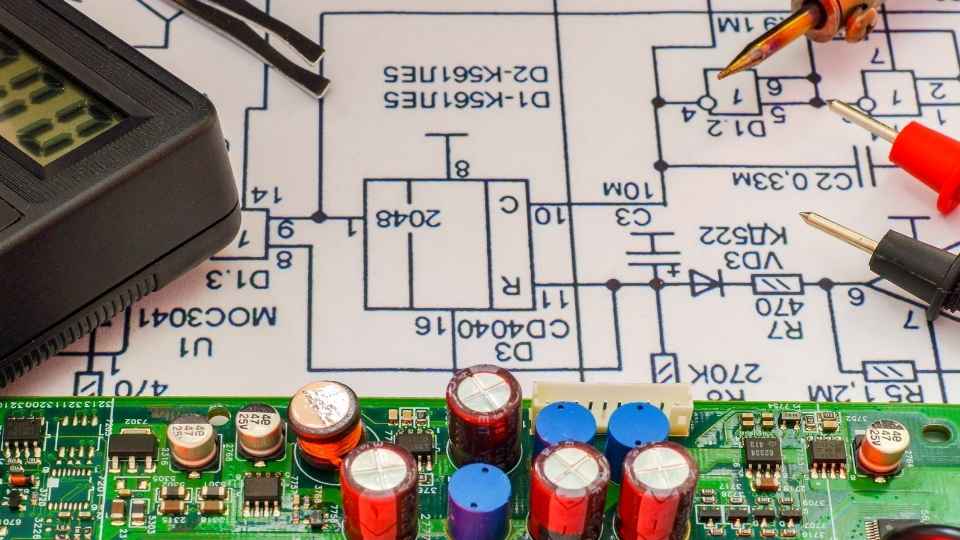
Implementing strict quality control protocols throughout the production line, including visual inspections and functional tests at various stages.
Conducting thorough reliability testing on finished products to simulate real-world conditions and assess their performance under different scenarios.
Strategies for Tracking and Resolving Defects in Electronics Products
To ensure the reliability of electronics products, it is crucial to have effective strategies in place for tracking and resolving defects. This involves meticulous monitoring and analysis of product performance throughout its lifecycle.
One strategy is implementing a robust defect tracking system that allows for the identification and documentation of any issues that arise during manufacturing or testing processes. This enables timely resolution and prevents potential defects from reaching the customers.
Additionally, conducting thorough root cause analysis is essential for identifying the underlying factors contributing to defects. By analyzing data, performing failure mode analysis, and utilizing statistical techniques, quality assurance engineers can pinpoint the root causes of defects and implement targeted corrective actions.
Furthermore, establishing effective communication channels with suppliers and customers can aid in defect resolution by enabling prompt feedback exchange and collaboration on investigations.
By implementing these strategies, companies can effectively track and resolve defects in their electronics products, ensuring high-quality standards are met.
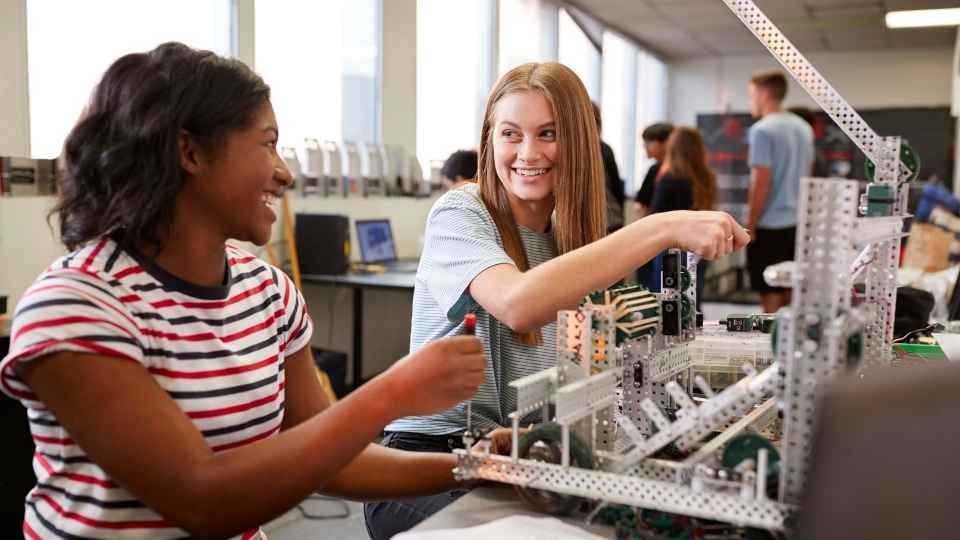
Transitioning into the subsequent section about 'best practices for ensuring long-term electronics reliability,' let's explore some key approaches to ensure lasting product performance.
Best Practices for Ensuring Long-Term Electronics Reliability
One crucial aspect of maintaining long-term performance in electronics is conducting regular maintenance and inspections to identify any potential issues or wear-and-tear. This ensures that the electronic devices continue to function optimally and have a longer lifespan.
To ensure long-term electronics reliability, it is essential to follow best practices such as:
- Keeping the electronics clean by regularly removing dust and debris.
- Checking for loose connections or damaged cables that can affect performance.
- Updating software and firmware regularly to benefit from bug fixes and improvements.
- Monitoring temperature levels to prevent overheating, which can cause damage.
By adhering to these best practices, users can enjoy the freedom of using their electronics without worrying about frequent breakdowns or reduced performance.
Regular maintenance and inspections are key in ensuring the longevity of electronic devices, ultimately providing users with reliable functionality for an extended period.
Frequently Asked Questions
What Is the Average Cost of Implementing Quality Control Measures in Electronics Manufacturing?
The average cost of implementing quality control measures in electronics manufacturing can vary significantly depending on factors such as the complexity of the product, size of the facility, and level of automation.
How Can a Company Ensure Long-Term Electronics Reliability While Keeping Costs Low?
Ensuring long-term electronics reliability while maintaining low costs requires a comprehensive approach. This includes rigorous quality control measures, thorough product validation processes, and continuous improvement initiatives to identify and address potential issues early on in the manufacturing process.
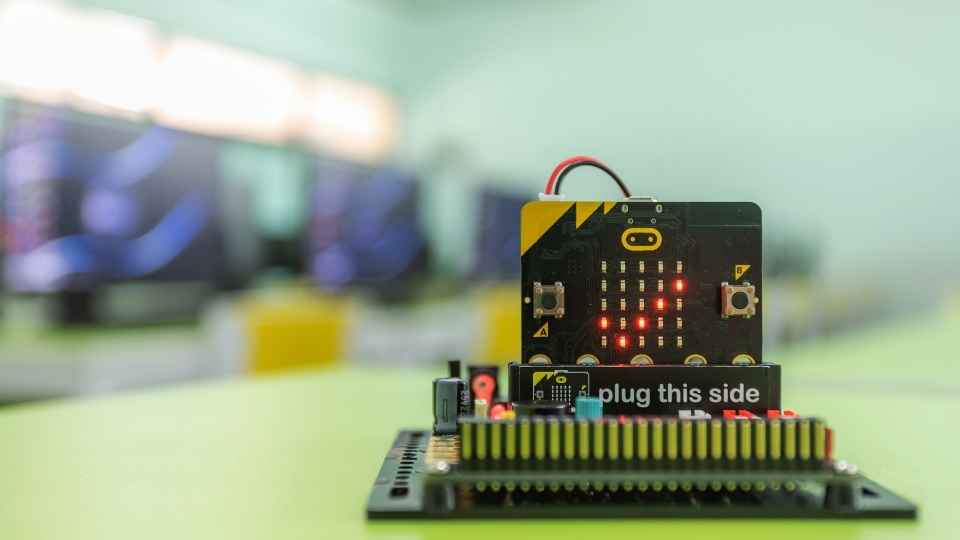
Are There Any Specific Certifications or Qualifications Required to Become a Quality Assurance Engineer in the Electronics Industry?
To become a quality assurance engineer in the electronics industry, specific certifications and qualifications are often required. These may include knowledge of industry standards, experience with testing methodologies, and proficiency in relevant software tools.
What Are Some Common Challenges Faced by Quality Assurance Engineers in the Electronics Industry?
Quality assurance engineers in the electronics industry face various challenges, including ensuring product reliability, managing complex testing processes, meeting regulatory standards, and adapting to rapid technological advancements. It requires meticulous attention to detail and staying up-to-date with industry trends.
How Can Reliability Analysis Data Be Used to Improve the Design and Development Process of Electronics Products?
Reliability analysis data plays a crucial role in enhancing the design and development process of electronics products. By analyzing this data, engineers can identify weaknesses, make informed design decisions, and implement necessary improvements to ensure higher reliability and customer satisfaction.