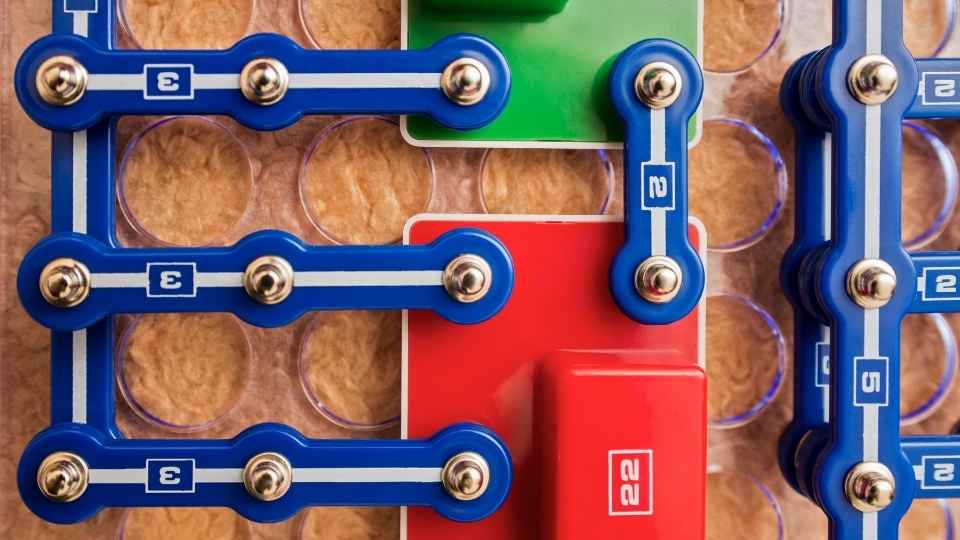
In the realm of manufacturing, success lies in the ability to seamlessly blend innovation and efficiency. Design for manufacturability (DFM) is a crucial concept that ensures cost-effectiveness and quality production by integrating these principles from the very inception of a product's design.
By alluding to the intricate dance between creativity and practicality, this article explores key considerations, component selection strategies, placement techniques, assembly methods, quality control measures, and cost analysis factors that collectively work towards achieving high-quality and cost-effective manufacturing.
Whether you are an industry professional or an aspiring entrepreneur seeking freedom in your production endeavors, this comprehensive guide will equip you with the tools necessary to navigate the complex landscape of DFM.
Key Takeaways
- Material selection plays a crucial role in achieving cost-effective and quality production.
- Streamlining assembly processes and optimizing workflow can significantly reduce time and costs.
- Quality control is essential in manufacturing design to prevent costly rework or product recalls.
- Enhancing product reliability improves customer trust and reduces costs associated with returns or repairs.
Key Considerations for Cost-Effective Design
When designing for cost-effectiveness, it is crucial to consider key factors that can optimize the manufacturing process and minimize production costs. One of the primary considerations is material selection. Choosing the right materials can have a significant impact on both the initial production costs and the long-term expenses associated with maintenance and repairs. It is important to select materials that are not only affordable but also durable and readily available in the market.
Another important factor to consider is process efficiency. By analyzing each step of the manufacturing process, designers can identify areas where improvements can be made to reduce waste, increase productivity, and lower costs. This may involve implementing automation or streamlining workflows.
Furthermore, product simplification should be taken into account during design. Complex designs often require more time, resources, and expertise to manufacture, leading to higher production costs. By simplifying designs without compromising functionality or quality, manufacturers can save significantly on production expenses.
Overall, by considering these key factors - material selection, process efficiency, and product simplification - designers can create cost-effective designs that meet customer requirements while minimizing production costs.
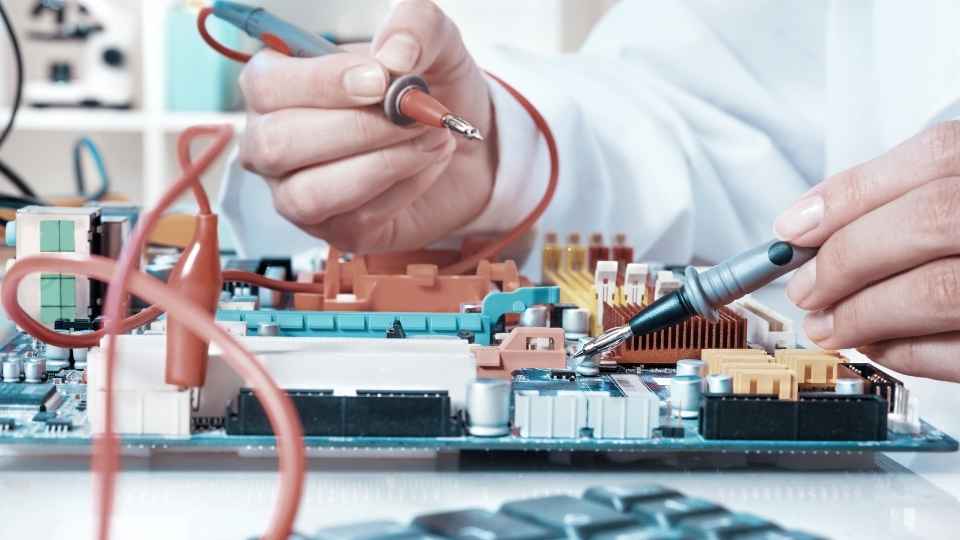
Optimizing Component Selection for Manufacturing Efficiency
To achieve efficient and streamlined manufacturing processes, a key consideration is the careful selection of components to optimize production efficiency. Component selection plays a crucial role in ensuring cost-effective and quality production. When selecting components, manufacturers must consider factors such as performance requirements, material compatibility, and ease of integration. Components that are specifically designed for manufacturability can greatly enhance efficiency by reducing assembly time and minimizing the risk of errors or defects.
Manufacturers should prioritize components that offer high reliability and durability while also being cost-effective. This requires thorough evaluation of various options available in the market. Additionally, the compatibility between different components should be assessed to ensure seamless integration within the manufacturing process.
Furthermore, it is important to consider component availability and lead times to avoid delays in production schedules. Collaborating closely with suppliers can provide insights into their manufacturing capabilities and help identify potential issues early on.
Essential Placement Considerations for Streamlined Production
When it comes to achieving streamlined production, essential placement considerations play a significant role.
Optimal component positioning is crucial in reducing assembly time and improving overall manufacturing efficiency.
Optimal Component Positioning
Achieving optimal component positioning is crucial for ensuring cost-effective and quality production in the realm of design for manufacturability. Proper placement of components plays a significant role in minimizing errors, reducing waste, and enhancing overall productivity. When components are accurately positioned, it allows for efficient assembly processes, reducing the chances of misalignment or rework. This not only saves time but also reduces costs associated with labor and materials.
To achieve optimal component positioning, designers need to consider factors such as size, shape, weight distribution, and compatibility with other components. Additionally, considerations must be made for accessibility during assembly processes to ensure ease of installation and maintenance.
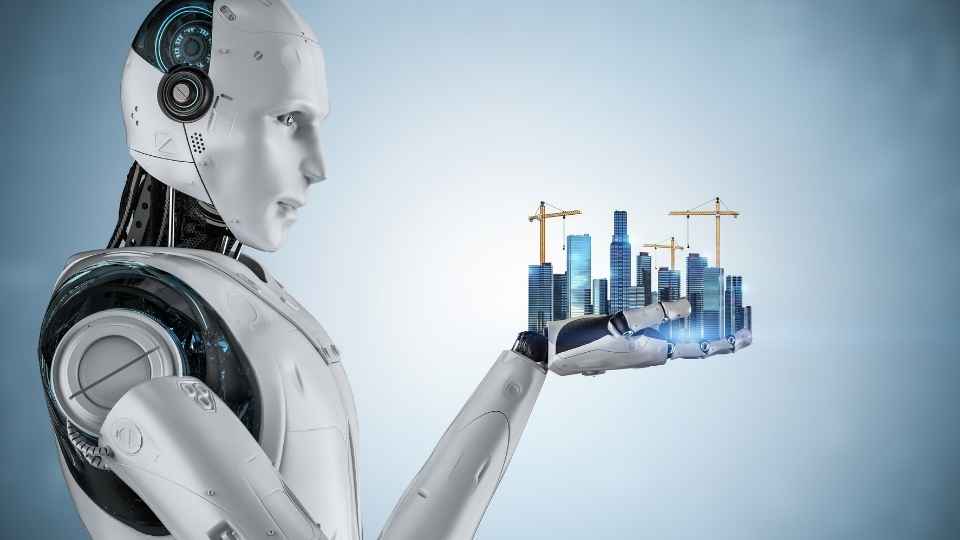
By focusing on achieving optimal component positioning during the design phase, manufacturers can streamline their production processes and improve product quality while minimizing potential issues that may arise during assembly.
Next, we will discuss another important aspect of design for manufacturability: minimizing assembly time.
Minimizing Assembly Time
Minimizing assembly time is a crucial factor in enhancing efficiency and productivity within the manufacturing process. By reducing the time required for assembling components, manufacturers can improve their overall production output and meet customer demands more effectively.
One way to achieve this is by implementing streamlined assembly processes that eliminate unnecessary steps and optimize workflow. This can be done through careful analysis of each assembly step, identifying potential bottlenecks or areas for improvement, and implementing changes accordingly.
Additionally, investing in automated assembly technologies can significantly reduce assembly time by eliminating manual labor and increasing precision. By leveraging these advancements, manufacturers can not only save time but also improve product quality and reduce costs.
Mastering assembly techniques for quality and efficiency is essential to achieving these goals.
Mastering Assembly Techniques for Quality and Efficiency
To ensure the highest level of quality and efficiency in assembly processes, it is crucial to master advanced techniques.
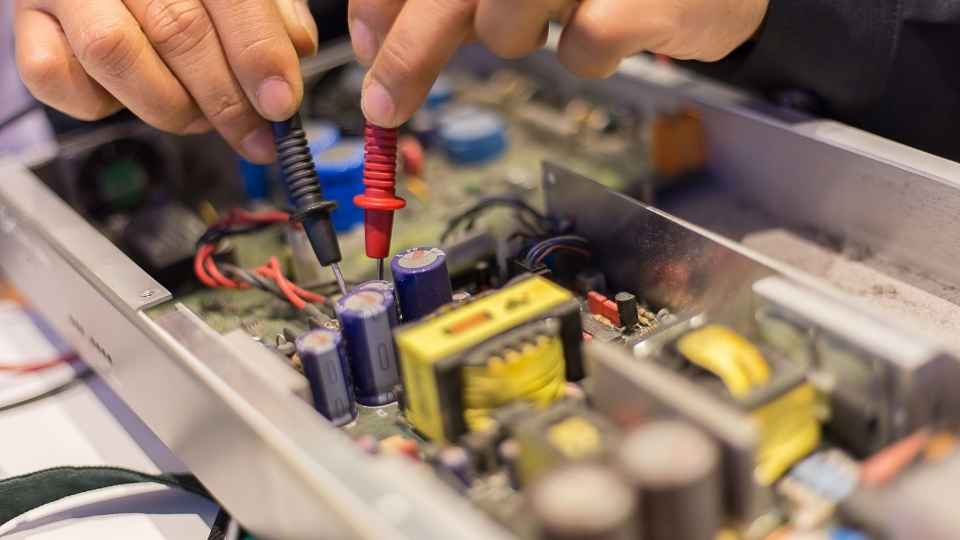
These techniques involve precise alignment, proper fastening methods, and optimal use of tools and equipment.
Streamlining Assembly Processes
One effective method for optimizing assembly processes involves analyzing the workflow and identifying areas where efficiency can be improved. By evaluating each step in the assembly process, it is possible to identify bottlenecks, redundancies, and areas of waste that can hinder productivity. This analysis can be done by conducting time studies, observing worker movements, or using simulation software to model and analyze the workflow.
Once the inefficiencies have been identified, steps can be taken to streamline the assembly process. This may involve rearranging workstations to minimize movement or implementing lean manufacturing principles to eliminate waste. Additionally, automation technologies such as robotics or conveyor systems can be introduced to increase efficiency and reduce manual labor.
Regular monitoring and continuous improvement efforts are essential for maintaining optimized assembly processes. By regularly reviewing workflows and making adjustments as needed, manufacturers can ensure that their assembly operations remain efficient and productive while delivering high-quality products to customers.
Enhancing Product Reliability
Enhancing product reliability involves implementing rigorous testing and quality control measures to identify and address potential issues before products are released to the market. This is crucial in ensuring customer satisfaction, minimizing warranty claims, and maintaining a strong brand reputation.
To achieve this, manufacturers employ various techniques such as environmental stress testing, accelerated life testing, and statistical analysis. These methods help simulate real-world conditions, evaluate product performance under different scenarios, and predict failure rates.
Additionally, quality control processes such as inspections, functional tests, and statistical process control are used to monitor production lines and ensure adherence to design specifications.
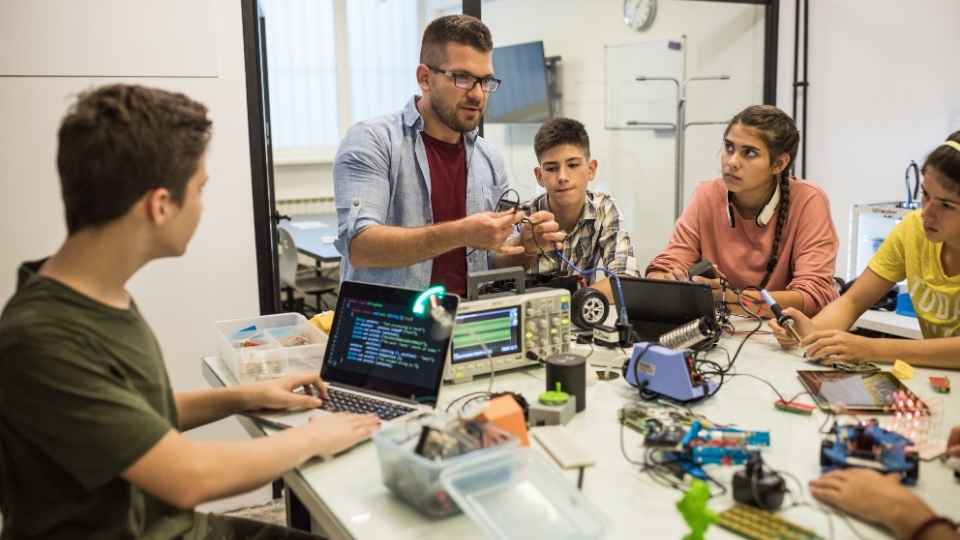
By incorporating these measures into the manufacturing process, companies can improve product reliability by identifying weaknesses early on and implementing necessary improvements or modifications before products reach consumers.
Ultimately, enhancing product reliability enhances customer trust in the brand while reducing costs associated with returns or repairs.
The Role of Quality Control in Manufacturing Design
Quality control plays a crucial role in ensuring cost-effective and quality production in manufacturing design. It involves monitoring and inspecting various aspects of the production process to identify any deviations from the desired standards. By implementing rigorous quality control measures, manufacturers can detect and rectify defects early on, preventing costly rework or product recalls.
One of the key components of quality control is statistical process control (SPC), which involves collecting and analyzing data to monitor the stability and capability of manufacturing processes. This enables manufacturers to identify potential issues before they result in defective products.
Additionally, quality control encompasses various inspection techniques such as visual inspection, dimensional measurement, and non-destructive testing. These techniques help verify that the manufactured products meet specified criteria for dimensions, tolerances, surface finish, functionality, and reliability.
Implementing effective quality control practices not only ensures that products meet customer expectations but also improves overall efficiency by reducing waste and rework. It helps manufacturers maintain a competitive edge in today's global market where customers demand high-quality products at affordable prices.
Analyzing the Cost Factors of Production for Effective Budgeting
To effectively manage the expenses associated with production, it is crucial to thoroughly analyze the various factors that contribute to costs. By understanding the cost drivers in manufacturing processes, businesses can make informed decisions to ensure cost-effective production without compromising on quality.
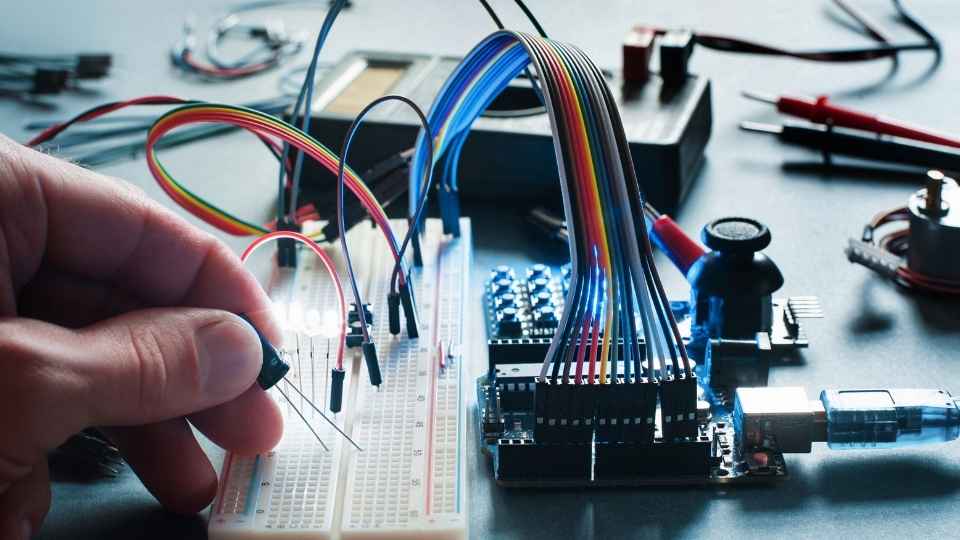
Some of the key factors that need to be analyzed include:
- Raw material costs
- Labor expenses
- Overhead expenditures
- Equipment maintenance and depreciation
Additionally, careful consideration should be given to waste management and energy consumption during production as these can significantly impact costs.
Conducting a comprehensive analysis of these factors allows for effective budgeting and resource allocation. This helps businesses optimize their operations while delivering high-quality products at competitive prices.
Strategies for Achieving High-Quality and Cost-Effective Manufacturing
Implementing efficient manufacturing strategies is essential for achieving both high-quality products and cost-effectiveness in production. One such strategy is adopting a design for manufacturability (DFM) approach. DFM focuses on designing products that are easy to manufacture, assemble, and test. By considering manufacturing constraints early in the design phase, companies can minimize production costs while maintaining product quality.
DFM involves various techniques such as simplifying designs, standardizing components, and reducing the number of parts. Simplification helps minimize the complexity of assembly processes and reduces the chances of errors or defects. Standardization allows for bulk purchasing and streamlines production by using common components across different products. Additionally, reducing the number of parts simplifies inventory management and improves overall efficiency.
By incorporating DFM principles into product development, manufacturers can achieve significant cost savings through improved production processes and reduced material waste. Moreover, it ensures that high-quality standards are met consistently throughout the manufacturing process.
Frequently Asked Questions
How Can Design for Manufacturability Help Reduce Production Costs?
Design for manufacturability can reduce production costs by optimizing the design process to ensure efficient and cost-effective manufacturing. By considering factors such as material selection, assembly methods, and production techniques, companies can minimize waste, improve productivity, and ultimately lower production costs.
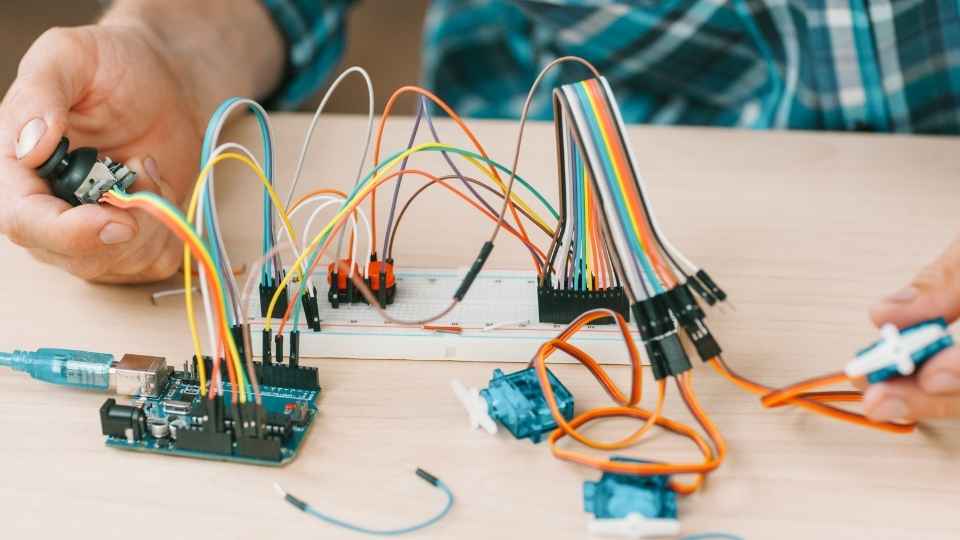
What Are the Key Factors to Consider When Selecting Components for Manufacturing Efficiency?
When selecting components for manufacturing efficiency, it is crucial to consider factors such as compatibility with existing systems, reliability, durability, and cost-effectiveness. These considerations ensure optimized production processes and enhanced product quality.
How Can Proper Placement Considerations Streamline the Production Process?
Proper placement considerations are crucial in streamlining the production process. By strategically arranging components, manufacturers can optimize workflow, reduce assembly time, and minimize errors, resulting in increased efficiency and cost-effectiveness.
What Are Some Assembly Techniques That Can Improve Both Quality and Efficiency?
Some assembly techniques that can improve both quality and efficiency include automated processes, standardized work instructions, error-proofing methods, continuous training and improvement programs, and effective communication among all stakeholders involved in the production process.
How Does Quality Control Play a Role in Manufacturing Design and Ensuring a High-Quality Final Product?
Quality control plays a crucial role in manufacturing design by ensuring that the final product meets specified standards. Through rigorous inspection, testing, and monitoring processes, it helps identify and rectify any deviations or defects that might compromise the quality of the end product.